Preparation method of phosphorus-nitrogen intumescent flame retardant
An intumescent flame retardant, phosphorus-nitrogen technology, applied in the field of flame retardant preparation, can solve the problems of poor compatibility, moisture absorption, large addition amount, etc., achieve good flame retardancy, reduce moisture absorption, weather resistance good effect
- Summary
- Abstract
- Description
- Claims
- Application Information
AI Technical Summary
Problems solved by technology
Method used
Image
Examples
Embodiment 1
[0018] Add phenylphosphorous dichloride (8.950g, 0.05mol) and 50ml ethyl acetate to a 250ml four-neck flask equipped with a thermometer, nitrogen gas introduction, 100ml constant pressure dropping funnel, magneton, reflux condenser and tail gas absorption device , Dissolve p-phenylenediamine (5.407g, 0.05mol) in 50ml ethyl acetate, and add it to the constant pressure funnel. Under nitrogen protection and stirring, the p-phenylenediamine solution was slowly added dropwise. After the dropwise addition was completed, the temperature was raised to reflux temperature and the reaction was continued for 3 hours, and after the reaction was completed, the nitrogen was continued. 2 Bring to room temperature. Then the mixture was suction-filtered under reduced pressure, and the filter cake was washed with 100 ml of ethyl acetate, and vacuum-dried at 100° C. for 5 hours to obtain 9.15 g of lavender solid, with a yield of 85.4%.
Embodiment 2
[0020] Add phenyl phosphorus dichloride (8.950g, 0.05mol) and 50ml of dichloromethane to a 250ml four-neck flask equipped with a thermometer, nitrogen gas introduction, 100ml constant pressure dropping funnel, magneton, reflux condenser and tail gas absorption device , Dissolving p-phenylenediamine (5.407g, 0.05mol) in 50ml of dichloromethane was added to a constant pressure funnel. Under nitrogen protection and stirring, the p-phenylenediamine solution was slowly added dropwise. After the dropwise addition, the temperature was raised to the reflux temperature to continue the reaction for 5 hours, and after the reaction was completed, the nitrogen was continued. 2 Bring to room temperature. Then the mixture was suction-filtered under reduced pressure, and the filter cake was washed with 100 ml of dichloromethane, and vacuum-dried at 100° C. for 5 hours to obtain 8.73 g of a lavender solid, with a yield of 81.5%.
Embodiment 3
[0022] Add phenylphosphorus dichloride (26.85g, 0.15mol) and 100ml chloroform to a 250ml four-neck flask equipped with a thermometer, nitrogen gas introduction, 100ml constant pressure dropping funnel, magneton, reflux condenser and tail gas absorption device. p-Phenylenediamine (16.22g, 0.15mol) was dissolved in 100ml of chloroform and added to the constant pressure funnel. Under nitrogen protection and stirring, the p-phenylenediamine solution was slowly added dropwise. After the dropwise addition, the temperature was raised to the reflux temperature to continue the reaction for 5 hours, and after the reaction was completed, the nitrogen was continued. 2 Bring to room temperature. Then the mixture was suction-filtered under reduced pressure, and the filter cake was washed with 200ml of chloroform, and dried in vacuum at 100°C for 5 hours to obtain 25.83g of lavender solid, with a yield of 80.4%.
PUM
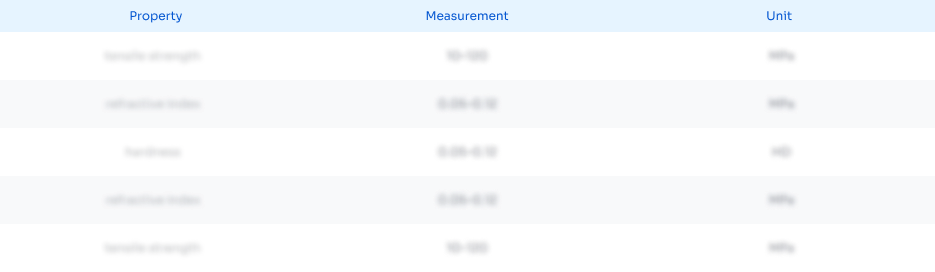
Abstract
Description
Claims
Application Information

- R&D Engineer
- R&D Manager
- IP Professional
- Industry Leading Data Capabilities
- Powerful AI technology
- Patent DNA Extraction
Browse by: Latest US Patents, China's latest patents, Technical Efficacy Thesaurus, Application Domain, Technology Topic, Popular Technical Reports.
© 2024 PatSnap. All rights reserved.Legal|Privacy policy|Modern Slavery Act Transparency Statement|Sitemap|About US| Contact US: help@patsnap.com