Beta-aminopropionitrile consecutive reaction process
A technology of aminopropionitrile and reaction, applied in the field of synthesis of organic compounds, can solve the problems of low selectivity of β-aminopropionitrile, high content of by-products, decreased selectivity, etc., to achieve enhanced selectivity, strong reaction selectivity, Effect of Yield Improvement
- Summary
- Abstract
- Description
- Claims
- Application Information
AI Technical Summary
Problems solved by technology
Method used
Image
Examples
Embodiment 1
[0037] Add 1500L of ammonia water with a content of 35% to the 2000L ammonia distribution kettle 1, and then add 100L of the phase transfer catalyst of the mixture of isopropanol and n-propanol configured in proportion; add 240kg of acrylonitrile into the acrylonitrile storage tank 2; Connect the ammonia water and acrylonitrile to the two inlets of the proportional pump 3 respectively, and enter the pipeline reactor 4 according to the volume ratio of ammonia water: acrylonitrile = 5:1. The ammonia water first passes through the preheating section, and then mixes with acrylonitrile and enters the reactor In the section, circulating water is used to control the temperature to ensure that the temperature of the reactor is 100-150°C and the pressure is below 1.0MPa. Ammonia, the material at the bottom of the tower is continuously transferred to the decompression ammonia flooding kettle 6 for further decompression and decompression of ammonia. After the ammonia flooding, the materia...
Embodiment 2
[0040] When testing in the laboratory, add 1500ml of ammonia water with a content of 35% to the 2000ml constant pressure funnel, and then add 100ml of the phase transfer catalyst of the mixture of isopropanol and n-propanol configured in proportion; Add 240g of acrylonitrile; connect the ammonia water and acrylonitrile to the two inlets of the proportional pump respectively, and enter the pipeline reactor according to the volume ratio of ammonia water: acrylonitrile = 5:1. The ammonia water first passes through the preheating section, and then mixes with acrylonitrile Enter the reactor section, use circulating water to control the temperature, ensure that the reactor temperature is 100-150°C, and the pressure is below 1.0MPa to react. After passing through the pipeline reactor, the material is decompressed to 0.05MPa through the pressure reducing valve and enters the ammonia removal tower In addition to ammonia, the material at the bottom of the tower is continuously transferre...
Embodiment 3
[0043]Add 750L of ammonia liquor with a content of 35% configured in the ammonia distribution kettle, then add 50L of a mixture phase transfer catalyst of isopropanol and n-propanol configured in proportion; add 120kg of acrylonitrile to acrylonitrile storage tank 2; mix ammonia liquor and Acrylonitrile is respectively connected to the two inlets of the proportional pump 3, and enters the pipeline reactor 4 according to the volume ratio of ammonia water: acrylonitrile=5:1. The ammonia water first passes through the preheating section, and then mixes with acrylonitrile and enters the reactor section. The temperature of the circulating water is controlled to ensure that the temperature of the reactor is 100-150°C and the pressure is below 1.0MPa. The material is continuously transferred to the decompression ammonia flooding kettle 6 for further decompression and ammonia flooding. After the ammonia flooding is completed, the material continuously enters the water distillation towe...
PUM
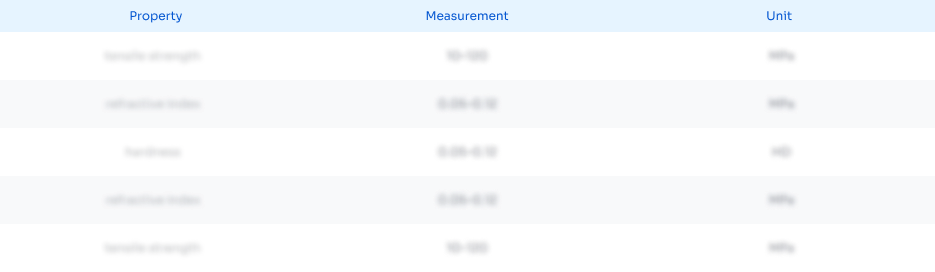
Abstract
Description
Claims
Application Information

- R&D
- Intellectual Property
- Life Sciences
- Materials
- Tech Scout
- Unparalleled Data Quality
- Higher Quality Content
- 60% Fewer Hallucinations
Browse by: Latest US Patents, China's latest patents, Technical Efficacy Thesaurus, Application Domain, Technology Topic, Popular Technical Reports.
© 2025 PatSnap. All rights reserved.Legal|Privacy policy|Modern Slavery Act Transparency Statement|Sitemap|About US| Contact US: help@patsnap.com