Low smoke halogen-free flame retardant sheath material for optical fiber cable, and preparation method thereof
A flame-retardant sheath and optical cable technology, applied in the direction of fiber mechanical structure, etc., can solve the problems of reducing mechanical properties and extrusion performance, and achieve excellent comprehensive performance, prevent the formation of molten droplets, and good cold resistance.
- Summary
- Abstract
- Description
- Claims
- Application Information
AI Technical Summary
Problems solved by technology
Method used
Image
Examples
Embodiment 1
[0040] (a). Take 1.2 parts of carbon black to make a masterbatch, add 58.2 parts of base material and mix;
[0041] (b). Surface treatment of the flame retardant with the coupling agent: first dry 30 parts of the flame retardant until the water content is less than 0.5%, then add 1 part of the coupling agent and 30 parts of the flame retardant into the mixer at the same time, Mix at 90°C for 8-10 minutes to modify the surface and further remove water;
[0042] (c). Mix 1.2 parts of carbon black masterbatch, 0.8 part of antioxidant, 0.8 part of plastic brightener, and 1.2 parts of softener for 10 minutes;
[0043] (d). The small dose of mixed material obtained in step (c) is added to the flame retardant treated with the coupling agent and mixed for 10 minutes;
[0044] (e). The mixture obtained in step (d) is added to PE and mixed uniformly;
[0045] (f). Then put the mixture in the step (d) into the extruder, masticate in the extruder, the masticating temperature is 170° C.,...
Embodiment 2
[0048] (a). Take 1.5 parts of carbon black to make a masterbatch, add 60 parts of base material and mix;
[0049] (b). Surface treatment of the coupling agent on the flame retardant: first dry 32 parts of the flame retardant until the water content is less than 0.5%, then add 0.8 parts of the coupling agent and 32 parts of the flame retardant into the mixer at the same time, Mix at 90°C for 8-10 minutes to modify the surface and further remove water;
[0050] (c). Mix 1.5 parts of carbon black masterbatch, 1.5 parts of antioxidant, 1.2 parts of plastic brightener, and 1.5 parts of softener for 10 minutes;
[0051] (d). The small dose of mixed material obtained in step (c) is added to the flame retardant treated with the coupling agent and mixed for 10 minutes;
[0052] (e). The mixture obtained in step (d) is added to PE and mixed uniformly;
[0053] (f). Then put the mixture in the step (d) into the extruder, masticate in the extruder, the masticating temperature is 170° C....
Embodiment 3
[0056] (a). Take 2 parts of carbon black to make a masterbatch, add 62 parts of base material and mix;
[0057] (b). Surface treatment of the flame retardant by the coupling agent: first dry 29 parts of the flame retardant until the water content is less than 0.5%, then add 1.6 parts of the coupling agent and 29 parts of the flame retardant into the mixer at the same time, Mix at 90°C for 8-10 minutes to modify the surface and further remove water;
[0058] (c). Mix 2 parts of carbon black masterbatch, 1.8 parts of antioxidant, 1.6 parts of plastic brightener, and 2 parts of softening agent for 10 minutes;
[0059] (d). The small dose of mixed material obtained in step (c) is added to the flame retardant treated with the coupling agent and mixed for 10 minutes;
[0060] (e). The mixture obtained in step (d) is added to PE and mixed uniformly;
[0061] (f). Then put the mixture in the step (d) into the extruder, masticate in the extruder, the masticating temperature is 170° C...
PUM
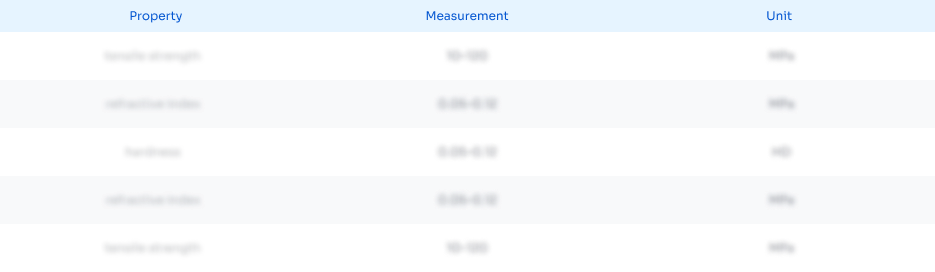
Abstract
Description
Claims
Application Information

- R&D
- Intellectual Property
- Life Sciences
- Materials
- Tech Scout
- Unparalleled Data Quality
- Higher Quality Content
- 60% Fewer Hallucinations
Browse by: Latest US Patents, China's latest patents, Technical Efficacy Thesaurus, Application Domain, Technology Topic, Popular Technical Reports.
© 2025 PatSnap. All rights reserved.Legal|Privacy policy|Modern Slavery Act Transparency Statement|Sitemap|About US| Contact US: help@patsnap.com