System for treating sulfur residue
A technology of sulfur slag and sulfur incineration furnace, which is applied in the direction of sulfur compounds, inorganic chemistry, non-metallic elements, etc., can solve the problems of high investment cost and low investment in additional equipment, and achieve the effect of convenient disassembly and cleaning, low investment and long service life
- Summary
- Abstract
- Description
- Claims
- Application Information
AI Technical Summary
Problems solved by technology
Method used
Image
Examples
Embodiment 1
[0030] A system for processing sulfur slag, comprising a fan 1, a drying tower 2 and a sulfur incinerator 3, the fan 1 is provided with an air inlet pipe 4 and an air outlet pipe 5, the outlet of the sulfur incinerator 3 and the fan 1 The air pipe 5 is connected, and the drying tower 2 is connected with the air inlet pipe 4 of the fan 1. The drying tower 2 is provided with a suction pipe 6, and the suction pipe 6 is provided with a suction port, and also includes a combustion furnace 7 and a flue 8 , One end of the flue 8 communicates with the combustion furnace 7 , and the other end communicates with the suction pipe 6 .
[0031] In the present invention, the flue 8 is provided with a filter 9, the filter 9 includes a housing, a filter screen 10 and a pressure plate 11, a filter cavity is provided inside the housing, and the filter screen 10 and the pressure plate 11 are all provided In the filter cavity, the filter cavity communicates with the flue 8 .
[0032] In the prese...
Embodiment 2
[0042] The difference from Embodiment 1 is that a sulfur filter 14 is provided on one side of the combustion furnace 7 .
[0043]When the present invention is in use, it can overcome the situation that the sulfur slag produced by the equipment in the prior art occupies the site, and the sulfur slag discharge place of the combustion furnace 7 is next to the sulfur filter 14, which is convenient for treating the sulfur slag; at the same time, it solves the problem of natural discharge of the sulfur slag potential safety hazards and environmental pollution.
Embodiment 3
[0045] The difference from Embodiments 1 and 2 is that: the combustion furnace 7 is provided with a three-layer furnace bridge 13; the filter screen 10 is one layer, and the pressing plate 11 is two pieces; the filter screen 10 is fixed between the two pressing plates 11 Between, filter screen 10 is compressed by two pressing plates 11.
PUM
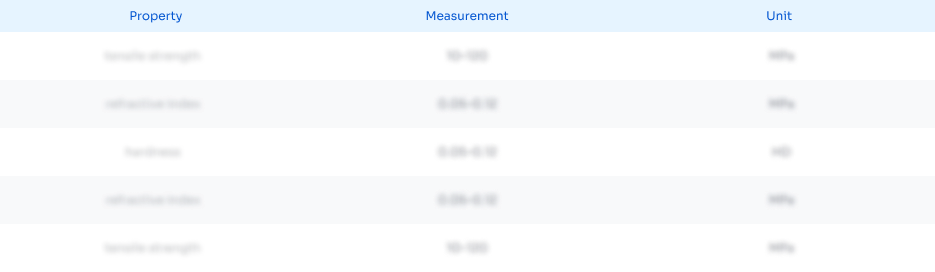
Abstract
Description
Claims
Application Information

- R&D
- Intellectual Property
- Life Sciences
- Materials
- Tech Scout
- Unparalleled Data Quality
- Higher Quality Content
- 60% Fewer Hallucinations
Browse by: Latest US Patents, China's latest patents, Technical Efficacy Thesaurus, Application Domain, Technology Topic, Popular Technical Reports.
© 2025 PatSnap. All rights reserved.Legal|Privacy policy|Modern Slavery Act Transparency Statement|Sitemap|About US| Contact US: help@patsnap.com