Operating method for numerical control system of numerical control machine tool
A technology of numerical control machine tools and numerical control systems, applied in the direction of digital control, electrical program control, etc., can solve the problems of large processing technology limitations, rigid human-computer interaction, and inability to modify processing parameters, and achieve the effect of expanding process capabilities
- Summary
- Abstract
- Description
- Claims
- Application Information
AI Technical Summary
Problems solved by technology
Method used
Image
Examples
Embodiment 1
[0043] Embodiment 1. Under the interactive method supported by the present invention, the craftsman can write an input dialog box when the part processing program starts, or after the CNC machine tool starts to execute the NC program and before the part processing program starts, requiring the operator to Input the number of repeated processing of parts and the interval time between repeated parts, and use the system variable to accept; the part program written after that can be cycled according to the number of times recorded in the system variable, that is, to realize batch processing of multiple identical parts.
Embodiment 2
[0044] Embodiment 2. Under the interactive method supported by the present invention, technicians can write an operator input dialog box when the part processing program starts, or after the CNC machine tool starts to execute the NC program and before the part processing program starts, requiring operation The operator enters his job number, accepts the job number string with the system variable, and then uses the file output command to include the operator’s job number and the processing start time into the file; before the end of the part program, combine the macro instruction to realize the End time and time difference calculation, write the file output command, and include the processing time into the file, which realizes the statistics of processing man-hours.
Embodiment 3
[0045] Embodiment 3. For the processing of parts with the same shape, different cutting parameters may be required due to different workpiece materials and tool materials. Under the interactive method supported by the present invention, the craftsman can write two input dialog boxes when the part processing program starts, or after the CNC machine tool starts to execute the NC program and before the part processing program starts, requiring the operator to input the workpiece respectively. Material and tool material, and use the system variable to accept the input result; after that, in the part processing program, according to the combination of the workpiece material and the tool material represented by the system variable recorded in the input dialog box, in the predetermined cutting amount recorded in the processing program by the craftsman Carry out optimization, enter the corresponding system parameters, and apply it to the subsequent part processing code to realize the s...
PUM
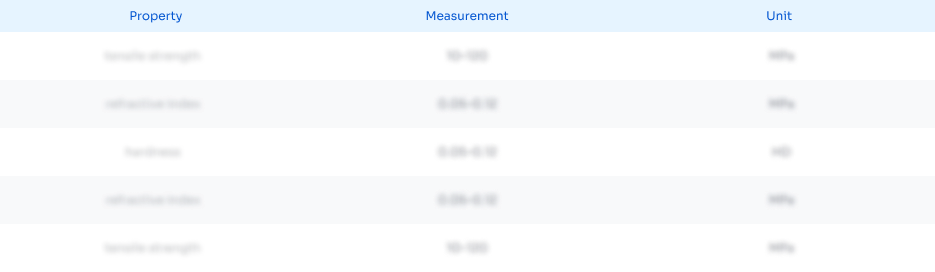
Abstract
Description
Claims
Application Information

- R&D
- Intellectual Property
- Life Sciences
- Materials
- Tech Scout
- Unparalleled Data Quality
- Higher Quality Content
- 60% Fewer Hallucinations
Browse by: Latest US Patents, China's latest patents, Technical Efficacy Thesaurus, Application Domain, Technology Topic, Popular Technical Reports.
© 2025 PatSnap. All rights reserved.Legal|Privacy policy|Modern Slavery Act Transparency Statement|Sitemap|About US| Contact US: help@patsnap.com