High-drawing speed continuous casting machine crystallizer copper plate electroplating process
A mold copper plate and electroplating process technology, applied in the field of electroplating, can solve the problems of reducing the operation rate of continuous casting machines, the quality of continuous casting slabs, the output, the increase in the number of repairs of the mold copper plates, and the strict control requirements of process conditions, etc. The effect of normal production operation, reduction of copper plate repair times and abnormal offline frequency, reduction of maintenance costs and maintenance workload
- Summary
- Abstract
- Description
- Claims
- Application Information
AI Technical Summary
Problems solved by technology
Method used
Image
Examples
Embodiment 1
[0068] Such as figure 1 , figure 2 , image 3 As shown, the present invention provides a high-speed continuous casting machine mold copper plate electroplating process that can increase the service life of the mold, improve the continuous casting machine operating rate and the quality of the slab.
[0069] The technical scheme adopted to achieve the above object is: a high-speed continuous casting machine crystallizer copper plate electroplating process, which includes the following steps:
[0070]a. Carry out degreasing treatment, mechanical sandblasting treatment, lye degreasing treatment, ultrasonic degreasing treatment on the copper plate substrate 1 after mechanical processing, and acid activate the surface of the coating to be coated;
[0071] b. Stick the lower part of the cleaned copper plate with insulating tape and put it into the electrolytic tank;
[0072] c. Put the anode 4 into the above-mentioned electroplating tank 5, and inject the electroplating solutio...
Embodiment 2
[0103] Such as figure 1 , figure 2 , image 3 As shown, the present invention provides a high-speed continuous casting machine mold copper plate electroplating process that can increase the service life of the mold, improve the continuous casting machine operating rate and the quality of the slab.
[0104] The technical scheme adopted to achieve the above object is: a high-speed continuous casting machine crystallizer copper plate electroplating process, which includes the following steps:
[0105] a. Carry out degreasing treatment, mechanical sandblasting treatment, lye degreasing treatment, ultrasonic degreasing treatment on the copper plate substrate 1 after mechanical processing, and acid activate the surface of the coating to be coated;
[0106] b. Stick the lower part of the cleaned copper plate with insulating tape and put it into the electrolytic tank;
[0107] c. Put the anode 4 into the above-mentioned electroplating tank 5, and inject the electroplating soluti...
Embodiment 3
[0137] Such as figure 1 , figure 2 , image 3 As shown, the present invention provides a high-speed continuous casting machine mold copper plate electroplating process that can increase the service life of the mold, improve the continuous casting machine operating rate and the quality of the slab.
[0138] The technical scheme adopted to achieve the above object is: a high-speed continuous casting machine crystallizer copper plate electroplating process, which includes the following steps:
[0139] a. Carry out degreasing treatment, mechanical sandblasting treatment, lye degreasing treatment, ultrasonic degreasing treatment on the copper plate substrate 1 after mechanical processing, and acid activate the surface of the coating to be coated;
[0140] b. Stick the lower part of the cleaned copper plate with insulating tape and put it into the electrolytic tank;
[0141] c. Put the anode 4 into the above-mentioned electroplating tank 5, and inject the electroplating soluti...
PUM
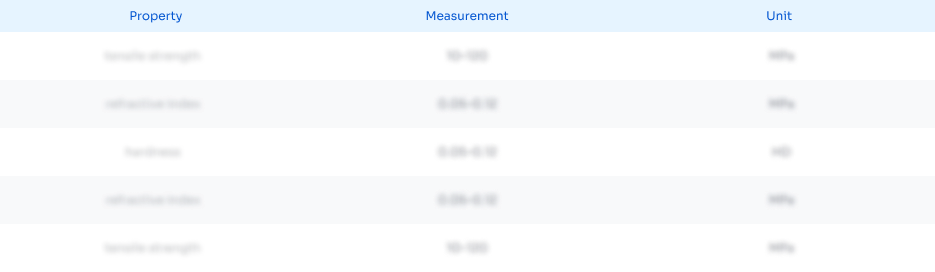
Abstract
Description
Claims
Application Information

- R&D Engineer
- R&D Manager
- IP Professional
- Industry Leading Data Capabilities
- Powerful AI technology
- Patent DNA Extraction
Browse by: Latest US Patents, China's latest patents, Technical Efficacy Thesaurus, Application Domain, Technology Topic, Popular Technical Reports.
© 2024 PatSnap. All rights reserved.Legal|Privacy policy|Modern Slavery Act Transparency Statement|Sitemap|About US| Contact US: help@patsnap.com