Polymetallic (iron, tin and zinc) ore comprehensive recovery beneficiation method
A technology of polymetallic ore and mineral processing methods, applied in chemical instruments and methods, wet separation, solid separation, etc., can solve the problems of environmental pollution of flotation wastewater, large consumption of flotation reagents, and complicated process flow, etc., and achieve reduction of flotation The comprehensive cost of dressing equipment and mineral processing is low, and the process is short
- Summary
- Abstract
- Description
- Claims
- Application Information
AI Technical Summary
Problems solved by technology
Method used
Image
Examples
Embodiment 1
[0018] Implementation 1: In this implementation, the iron-tin-associated zinc-tungsten-arsenic ore in a concentrator is used as the raw material for production.
[0019] The ore contains Sn0.63%, Fe33.33%, As0.94%, Zn0.53%. After the raw ore is ground, it undergoes a magnetic field strength of 1800 Oersted rough separation, and the magnetic product is ground and then passed through a magnetic field strength of 1000. Oersted's secondary concentration produces iron concentrate with a yield of 45.70%, a grade of 64.01%, and a recovery rate of 87.77%. The magnetic roughing tailings and the concentrated tailings are combined to undergo a sweep with a magnetic field strength of 1200 Oersted , the non-magnetic mineral materials are directly classified, and the coarse sand of +0.039mm is sorted on the first-stage shaking table and the re-washing shaker. The middle ore mill reaches 200 mesh, accounting for 70%, and it enters the second-stage shaking table and the re-washing shaker. The...
Embodiment 2
[0020] Implementation 2: The ore contains Sn0.67%, Fe34.17%, As1.04%, Zn0.57%. After the raw ore is ground, it undergoes magnetic separation with a magnetic field strength of 1800 Oersted, and the magnetic product is ground and then passed through a magnetic field. The secondary concentration of 1400 Oersted yields 45.13% iron concentrate with a grade of 65.22% and a recovery rate of 86.14%. The non-magnetic mineral materials are directly classified, and the coarse sand of +0.039mm is sorted by a shaking table and a rewashing shaking table. Heavy sand products are obtained by re-washing shaker separation; fine mud is subjected to rough separation by centrifuge, and belt chute is selected to obtain fine mud and heavy sand; heavy sand products are subjected to mixed flotation of zinc and arsenic; flotation foam is then separated from arsenic and zinc to produce grades Zinc concentrate with a grade of 45.74% and a recovery rate of 66.07%, and arsenic concentrate with a grade of 4...
Embodiment 3
[0021] Implementation 3: The ore contains Sn0.63%, Fe33.3%, As1.17%, Zn0.51%. After the raw ore is ground, it undergoes magnetic separation with a magnetic field strength of 1600 Oersted, and the magnetic product is ground through 1000 Oersted. The special secondary selection produces iron concentrate with a yield of 45.81%, a grade of 66.06%, and a recovery rate of 87.71%. The mineral material is directly classified, and the coarse sand of +0.039mm is sorted by the first-stage shaking table and the re-washing table. The heavy sand product is obtained; the fine mud is subjected to rough selection in a centrifuge, and the belt chute is selected to obtain fine mud and heavy sand; the heavy sand product is subjected to mixed flotation of zinc and arsenic; the flotation foam is then separated from arsenic and zinc, and the output grade is 46.66%, and the recovery rate is 69.06% % zinc concentrate, and arsenic concentrate with a grade of 59.16% and a recovery rate of 46.11%. The fl...
PUM
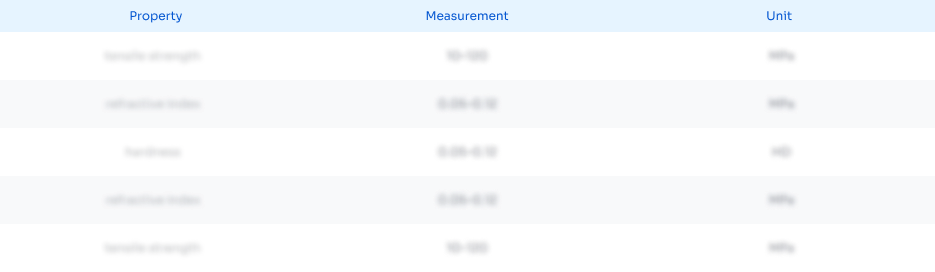
Abstract
Description
Claims
Application Information

- R&D
- Intellectual Property
- Life Sciences
- Materials
- Tech Scout
- Unparalleled Data Quality
- Higher Quality Content
- 60% Fewer Hallucinations
Browse by: Latest US Patents, China's latest patents, Technical Efficacy Thesaurus, Application Domain, Technology Topic, Popular Technical Reports.
© 2025 PatSnap. All rights reserved.Legal|Privacy policy|Modern Slavery Act Transparency Statement|Sitemap|About US| Contact US: help@patsnap.com