Production technology of Fe/N/C cathode for novel direct sodium borohydride fuel cell
A cathode and technology technology, applied in the field of electrode preparation, direct sodium borohydride fuel cell cathode preparation, can solve problems such as regulating the number of graphene layers, and achieve the effects of simplifying preparation technology, reducing production costs, and high power generation performance
- Summary
- Abstract
- Description
- Claims
- Application Information
AI Technical Summary
Problems solved by technology
Method used
Image
Examples
Embodiment 1
[0016] in such as figure 1 In the shown reactor, the nickel foam and carbon cloth double-layer rolls are placed on the left shaft, and the nickel foam and carbon cloth are pulled out through the middle reaction zone and fixed on the right winding mechanism. Vacuum the reactor to 10 -2 Pa and filled with nitrogen and then evacuated, repeated several times to make the residual oxygen in the reactor less than 10 -4 Pa. Raise the temperature of the intermediate reaction zone to 1050 o C. Start to feed the mixed gas of methane and nitrogen (the volume fraction of methane is 40%, and the gas fraction of nitrogen is 60%), and at the same time start the right drive winding mechanism to make the nickel foam and carbon cloth pass through the middle at a speed of 0.5 mm / min. In the reaction zone, graphene is grown on the surface of the nickel foam. When the nickel foam and carbon cloth are completely rolled up on the right side, stop heating and ventilation, and reduce the temp...
Embodiment 2
[0019] in such as figure 1 In the shown reactor, the nickel foam and carbon cloth double-layer rolls are placed on the left shaft, and the nickel foam and carbon cloth are pulled out through the middle reaction zone and fixed on the right winding mechanism. Vacuum the reactor to 10-2 Pa and filled with nitrogen and then evacuated, repeated several times to make the residual oxygen in the reactor less than 10 -4 Pa. Raise the temperature of the intermediate reaction zone to 1050 o C. Start to feed the mixed gas of methane and nitrogen (the volume fraction of methane is 20%, and the gas fraction of nitrogen is 80%), and at the same time start the right drive winding mechanism to make the nickel foam and carbon cloth pass through the middle at a speed of 5 mm / min. In the reaction zone, graphene is grown on the surface of the nickel foam. When the nickel foam and carbon cloth are completely rolled up on the right side, stop heating and ventilation, and reduce the temperat...
Embodiment 3
[0022] in such as figure 1 In the shown reactor, the nickel foam and carbon cloth are double-layered on the left shaft, and the nickel foam and carbon cloth are pulled out through the middle reaction zone and fixed on the right winding mechanism. Vacuum the reactor to 10 -2 Pa and filled with nitrogen and then evacuated, repeated several times to make the residual oxygen in the reactor less than 10 -4 Pa. Raise the temperature of the intermediate reaction zone to 1050 o C. Start to feed the mixed gas of methane and nitrogen (the volume fraction of methane is 40%, and the gas fraction of nitrogen is 60%), and at the same time start the right drive winding mechanism to make the nickel foam and carbon cloth pass through the middle continuously at a speed of 50 mm / min. In the reaction zone, graphene is grown on the surface of the nickel foam. When the nickel foam and carbon cloth are completely rolled up on the right side, stop heating and ventilation, and reduce the tem...
PUM
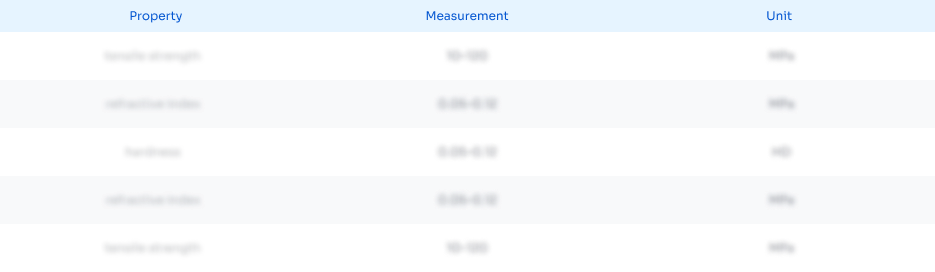
Abstract
Description
Claims
Application Information

- R&D
- Intellectual Property
- Life Sciences
- Materials
- Tech Scout
- Unparalleled Data Quality
- Higher Quality Content
- 60% Fewer Hallucinations
Browse by: Latest US Patents, China's latest patents, Technical Efficacy Thesaurus, Application Domain, Technology Topic, Popular Technical Reports.
© 2025 PatSnap. All rights reserved.Legal|Privacy policy|Modern Slavery Act Transparency Statement|Sitemap|About US| Contact US: help@patsnap.com