Planet magnetic meshing flexible transmission mechanism
A flexible transmission, magnetic meshing technology, applied in the direction of transmission, belt/chain/gear, mechanical equipment, etc., can solve the problems of inability to achieve impact torque absorption and torque limit protection transmission, loss, mechanical friction of gear transmission, etc. Work efficiency and reliability, no meshing noise, resizing effects
- Summary
- Abstract
- Description
- Claims
- Application Information
AI Technical Summary
Problems solved by technology
Method used
Image
Examples
Embodiment 1
[0026] Such as figure 1 As shown, a planetary magnetic meshing flexible transmission device includes a housing, a planetary magnetic wheel assembly, an outer magnetic coil assembly, and a central magnetic wheel assembly, and the planetary magnetic wheel assembly, the outer magnetic coil assembly, and the central magnetic wheel assembly are all arranged in the housing, The outer magnetic coil assembly is connected with the housing. Corresponding bearings are arranged between the planetary magnetic wheel assembly and the central magnetic wheel assembly, between the planetary magnetic wheel assembly and the casing, and between the central magnetic wheel assembly and the casing.
[0027] The planetary magnetic wheel assembly includes the planetary carrier shaft extension 1, the planetary carrier 2 and three sets of symmetrically distributed planetary magnetic wheel sets (such as image 3 shown). The shaft extension 1 of the planetary carrier is connected with the planetary carri...
Embodiment 2
[0035] This embodiment is basically the same as Embodiment 1, the difference is: as figure 2 , Figure 4 As shown, the present embodiment is provided with four groups of symmetrically distributed planetary magnetic wheel sets, and the relationship between the axial arrangement number W of the outer magnetic ring, the axial arrangement number X of the planetary magnetic wheels and the axial arrangement number Z of the central magnetic wheel is X=W+ 1=Z+1, W:X:Z=3:4:3. Such as figure 2 As shown, in this embodiment, planetary magnetic yokes 13 are arranged on the outermost planetary magnet wheels in a staggered arrangement.
PUM
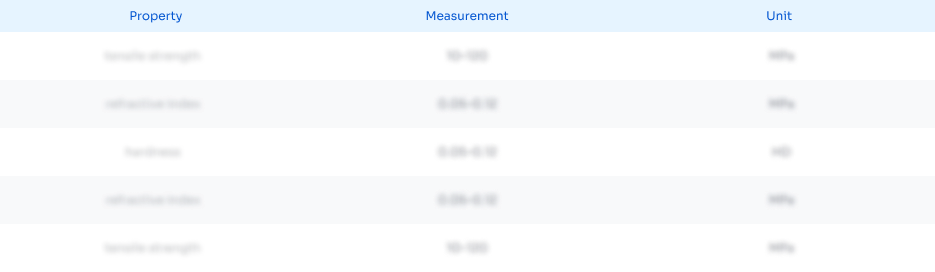
Abstract
Description
Claims
Application Information

- R&D
- Intellectual Property
- Life Sciences
- Materials
- Tech Scout
- Unparalleled Data Quality
- Higher Quality Content
- 60% Fewer Hallucinations
Browse by: Latest US Patents, China's latest patents, Technical Efficacy Thesaurus, Application Domain, Technology Topic, Popular Technical Reports.
© 2025 PatSnap. All rights reserved.Legal|Privacy policy|Modern Slavery Act Transparency Statement|Sitemap|About US| Contact US: help@patsnap.com