Method for melting nickel-base high temperature alloy with electro-slag furnace
A technology of nickel-based superalloys and superalloys, which is applied in the field of electroslag furnace smelting nickel-based superalloys, can solve the problems of easy cracking, segregation of steel ingots, poor thermal processing performance, etc. Good results
- Summary
- Abstract
- Description
- Claims
- Application Information
AI Technical Summary
Problems solved by technology
Method used
Examples
Embodiment 1
[0033] Alloy type: GH4169, Al 0.72% and Ti 0.95% in the electrode.
[0034] Crystallizer size: φ350×1650mm
[0035] The slag is five-element slag: CaF 2 50%, Al 2 o 3 22%, CaO 20%, MgO 5%, TiO 2 3%. Slag volume: 35kg
[0036] Ⅰ charge
[0037] Weld the φ280×2200mm GH4169 electrode with the dummy electrode and connect it with the electrode holder. At the bottom of the crystallizer, place the same material as the arc strike ring, turning chips and 3.5kg of slag.
[0038] Ⅱ inert gas purge
[0039] Close the protective cover, blow in Ar gas to purge the bottom of the furnace, the pressure of argon is 0.3 MPa, and open the smoke exhaust device at the same time to discharge the air in the furnace for 10 minutes.
[0040] Ⅲ protection smelting
[0041] Close the smoke exhaust valve, feed Ar gas into the crystallizer and the protective cover at a flow rate of 10ml / min, and maintain a slight positive pressure (1.05bar) in the protective cover.
[0042] Ⅳ arc slag
...
Embodiment 2
[0053] Alloy type: Al0.70% and Ti0.63% in Inconel690 electrode.
[0054] Crystallizer size: φ290×1650mm
[0055] The slag is ternary slag: CaF2 : 68%, Al 2 o 3 : 17%, CaO: 15%, slag amount 28kg
[0056] Ⅰ charge
[0057] Weld the φ220×1700mm Inconel690 electrode with the dummy electrode and connect it with the electrode holder. At the bottom of the crystallizer, place the same material as the arc ring, turning chips and 2.5kg of slag.
[0058] Ⅱ inert gas purge
[0059] Close the protective cover, blow in Ar gas to purify the bottom of the furnace, the argon pressure is 0.3 MPa, and open the smoke exhaust device at the same time to discharge the air in the furnace for 5 minutes.
[0060] Ⅲ protection smelting
[0061] Close the smoke exhaust valve, feed Ar gas into the crystallizer and the protective cover at a flow rate of 5 l / min, and maintain a slight positive pressure (1.08 bar) in the protective cover.
[0062] Ⅳ arc slag
[0063] The slag melting voltage ...
PUM
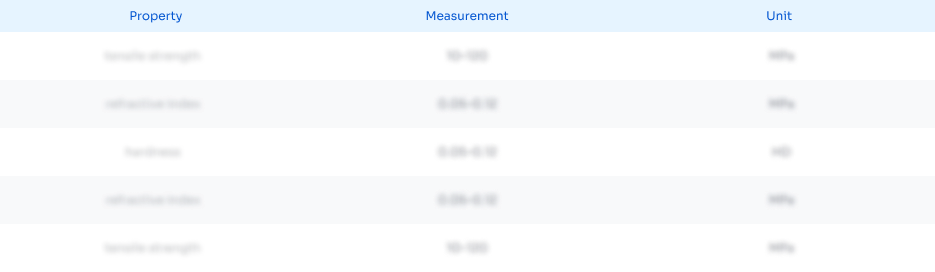
Abstract
Description
Claims
Application Information

- R&D
- Intellectual Property
- Life Sciences
- Materials
- Tech Scout
- Unparalleled Data Quality
- Higher Quality Content
- 60% Fewer Hallucinations
Browse by: Latest US Patents, China's latest patents, Technical Efficacy Thesaurus, Application Domain, Technology Topic, Popular Technical Reports.
© 2025 PatSnap. All rights reserved.Legal|Privacy policy|Modern Slavery Act Transparency Statement|Sitemap|About US| Contact US: help@patsnap.com