Preparing method of iron-based molding mixture
A mixture and iron-based technology, applied in metal processing equipment, transportation and packaging, etc., can solve problems such as poor fluidity, poor process performance of mixtures, and difficult solutions
- Summary
- Abstract
- Description
- Claims
- Application Information
AI Technical Summary
Problems solved by technology
Method used
Image
Examples
Embodiment 1
[0020] A method for preparing an iron-based molding compound, comprising the following steps:
[0021] (1) Weighing raw materials: respectively weigh iron powder, copper powder 18%, graphite 1%, spindle oil 0.08%, and zinc stearate 0.8% according to the formula requirements;
[0022] (2) Wetting the iron powder: Add the spindle oil to the iron powder and let it stand for 20-200min to form a wet iron powder;
[0023] (3) Mixing process: put the wetted iron powder and the graphite and lubricant weighed in (1) into the biconical mixer, and mix thoroughly; then add the copper powder into the mixer, fully Take out after mixing to obtain a mixture.
Embodiment 2
[0025] The difference between this embodiment and embodiment 1 is: the mixing process of the step (3) is: first add wet iron powder and graphite in the mixer, after fully mixing, then add copper powder, lubricant, fully Take out after mixing to obtain a mixture.
Embodiment 3
[0027] The difference between this embodiment and embodiment 1 is that the mixing process of the step (3) is as follows: first add the wet iron powder into the mixer, after fully mixing, add graphite, after fully mixing, then add copper powder , lubricant, fully mixed and then taken out to obtain a mixture.
PUM
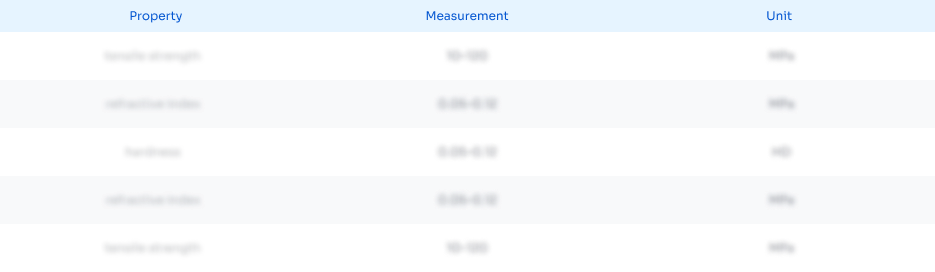
Abstract
Description
Claims
Application Information

- R&D
- Intellectual Property
- Life Sciences
- Materials
- Tech Scout
- Unparalleled Data Quality
- Higher Quality Content
- 60% Fewer Hallucinations
Browse by: Latest US Patents, China's latest patents, Technical Efficacy Thesaurus, Application Domain, Technology Topic, Popular Technical Reports.
© 2025 PatSnap. All rights reserved.Legal|Privacy policy|Modern Slavery Act Transparency Statement|Sitemap|About US| Contact US: help@patsnap.com