An Improved DC Bus Voltage Control Method for Two-Stage Converter
A technology of DC bus voltage and control method, which is applied in the direction of converting AC power input to DC power output, electrical components, single-network parallel feeding arrangement, etc., and can solve the problem of DC bus voltage impact, increased fluctuation, and deterioration of system dynamic performance, etc. question
- Summary
- Abstract
- Description
- Claims
- Application Information
AI Technical Summary
Problems solved by technology
Method used
Image
Examples
Embodiment Construction
[0018] The technical solution of the present invention will be further described in detail according to the accompanying drawings in the description.
[0019] The main circuit structure of the two-stage converter is as follows: figure 1 As shown, it includes the front-stage DC / DC power conversion unit and the rear-stage DC / AC power conversion unit, and finally connects to the grid or load through the LCL filter. The DC / DC module adopts independent PWM control mode: when the lower bridge arm performs PWM modulation and the upper bridge arm is turned off, the circuit is in the Boost discharge state; when the upper bridge arm performs PWM modulation and the lower bridge arm is turned off, the circuit is in the Buck charging state ; The DC / AC module uses space vector modulation (SVPWM).
[0020] The relationship between the voltage error vector caused by the dead zone effect on the DC / AC side and the inverter output current is as follows: figure 2 shown. Assuming that the angl...
PUM
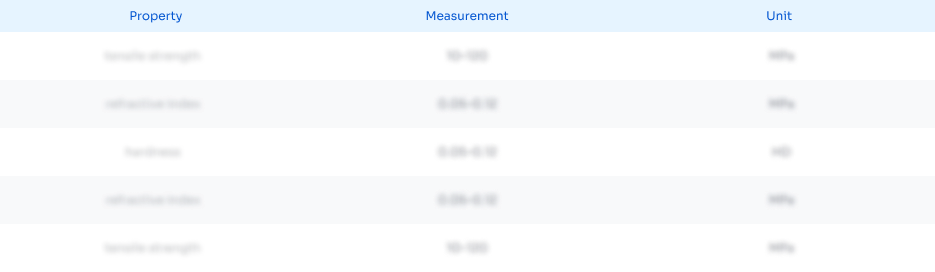
Abstract
Description
Claims
Application Information

- R&D
- Intellectual Property
- Life Sciences
- Materials
- Tech Scout
- Unparalleled Data Quality
- Higher Quality Content
- 60% Fewer Hallucinations
Browse by: Latest US Patents, China's latest patents, Technical Efficacy Thesaurus, Application Domain, Technology Topic, Popular Technical Reports.
© 2025 PatSnap. All rights reserved.Legal|Privacy policy|Modern Slavery Act Transparency Statement|Sitemap|About US| Contact US: help@patsnap.com