Welded connector
A connector, welding technology, applied in the direction of welding/welding connection, connection, conductive connection, etc., can solve the problems of long wiring process, short service life, slow transmission speed, etc., and achieve fast electrical transmission. And the effect of stability, short consumption time and low production cost
- Summary
- Abstract
- Description
- Claims
- Application Information
AI Technical Summary
Problems solved by technology
Method used
Image
Examples
Embodiment Construction
[0043] The present invention will be further described in conjunction with the following examples.
[0044] A welded connector of this embodiment such as Figure 1 to Figure 4 As shown, it includes a plastic body 1 and a connection terminal. The plastic body 1 is provided with a slot 11 for placing the connection terminal group 2. The connection terminal in the connection terminal group 2 includes a right-angle connection middle part 21, and an elastic body connected to one end of the right-angle connection middle part 21. The clamping portion 22 is connected to the other end of the right-angled connecting middle portion 21 with a strip-shaped sheet-shaped welding portion 23 , and the elastic clamping portion 22 is provided with a terminal locking protrusion 2211 for clamping the terminal to the slot 11 .
[0045] The present invention can directly weld the wiring terminal and the wire core of the cable 4 during wiring, which reduces the riveting process compared with the ...
PUM
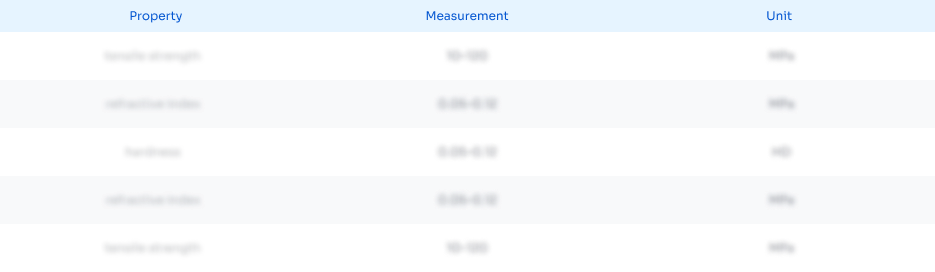
Abstract
Description
Claims
Application Information

- R&D Engineer
- R&D Manager
- IP Professional
- Industry Leading Data Capabilities
- Powerful AI technology
- Patent DNA Extraction
Browse by: Latest US Patents, China's latest patents, Technical Efficacy Thesaurus, Application Domain, Technology Topic, Popular Technical Reports.
© 2024 PatSnap. All rights reserved.Legal|Privacy policy|Modern Slavery Act Transparency Statement|Sitemap|About US| Contact US: help@patsnap.com