Method for reproducing paper pulp used for filter stick core paper by utilizing filter stick waste
A technology for filter rods and waste materials, which is applied in pulp beating/refining methods, washing/replacing pulp treatment fluids, papermaking, etc. It can solve the problems of health hazards for operators, strict requirements on impurity content, and poor stability of filter rod suction resistance, etc. Achieve the effect of mild impregnation conditions, high pulp yield and good uniformity
- Summary
- Abstract
- Description
- Claims
- Application Information
AI Technical Summary
Problems solved by technology
Method used
Image
Examples
Embodiment 1
[0031] Cut cellulose diacetate waste to 5mm, impregnate with water, the ratio of water addition (volume L) to waste (mass kg, dry, the same below) is 6:1, and pre-impregnate at 70°C for 10 minutes. Then impregnate the waste material in a sodium hydroxide solution with a concentration of 2g / L at 70°C. The amount of chemicals added to the waste filter rod is 2%, and the impregnation lasts for 15 minutes. The treated waste was refined with a disc refiner with a disc refiner gap of 0.2mm, a refining concentration of 10%, a refining temperature of 70°C, and a refining time of 15 minutes. The pulp obtained by disc refining is washed, screened and concentrated to obtain pulp. It has been determined that the pulp yield is 95%, the fiber length distribution is concentrated, the pulp is uniform, and there are no broken pieces of paper and bundled fibers.
Embodiment 2
[0033] Cut the mixed waste of cellulose diacetate filter rod and paper filter rod to 1mm, impregnate it with water, the ratio of the amount of water added (volume L) and the amount of waste (mass kg, dry, the same below) is 10:1, in 100 Pre-dipping at ℃ for 5min. Then impregnate the waste with chemicals in sodium hydroxide and sodium sulfite solutions with a concentration of 0.25g / L at 25°C. The addition of chemicals to the filter rod waste is 1% and 1%, respectively, and impregnate for 5 minutes. The treated waste was refined with a disc refiner with a disc refiner gap of 0.2mm, a refining concentration of 10%, a refining temperature of 25°C, and a refining time of 10 minutes. The pulp obtained by disc refining is washed, screened and concentrated to obtain pulp. It has been determined that the pulp yield is 97%, the fiber length distribution is concentrated, the pulp is uniform, and there are no broken pieces of paper and bundled fibers.
Embodiment 3
[0035]Cut the waste paper filter rod to 5mm, impregnate it with water, the ratio of the amount of water added (volume L) to the amount of waste (mass kg, dry, the same below) is 10:1, and pre-soak at 100°C for 10 minutes. Then impregnate the waste material in a sodium hydroxide solution at 50°C with a concentration of 1g / L. The amount of chemicals added to the filter rod waste material is 1%, and the impregnation lasts for 10 minutes. The treated waste was refined with a disc refiner with a disc refiner gap of 0.3mm, a refining concentration of 20%, a refining temperature of 50°C, and a refining time of 10 minutes. The pulp obtained by disc refining is washed, screened and concentrated to obtain pulp. It has been determined that the pulp yield is 94%, the fiber length distribution is concentrated, the pulp is uniform, and there are no broken pieces of paper and bundled fibers.
PUM
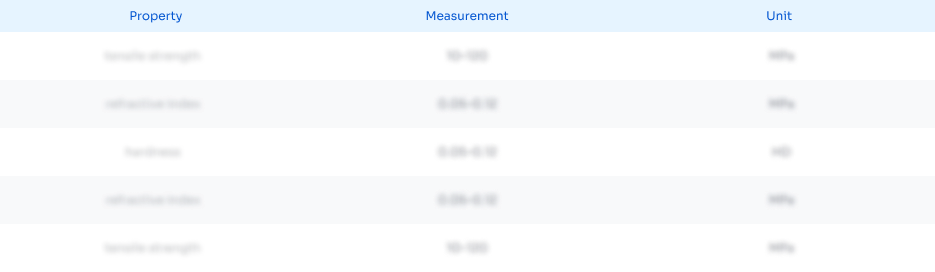
Abstract
Description
Claims
Application Information

- R&D
- Intellectual Property
- Life Sciences
- Materials
- Tech Scout
- Unparalleled Data Quality
- Higher Quality Content
- 60% Fewer Hallucinations
Browse by: Latest US Patents, China's latest patents, Technical Efficacy Thesaurus, Application Domain, Technology Topic, Popular Technical Reports.
© 2025 PatSnap. All rights reserved.Legal|Privacy policy|Modern Slavery Act Transparency Statement|Sitemap|About US| Contact US: help@patsnap.com