Preparation method of polyacrylonitrile pre-oxidation fiber and carbon fiber
A technology of polyacrylonitrile-based pre-oxidation fiber and polyacrylonitrile, which is applied to the chemical characteristics of fibers, textiles and papermaking, etc., can solve the problems of limiting the production efficiency of carbon fibers, complicated pre-oxidation process, etc., so as to improve the generation efficiency and shorten the heat treatment time. , the effect of rapid pre-oxidation
- Summary
- Abstract
- Description
- Claims
- Application Information
AI Technical Summary
Problems solved by technology
Method used
Image
Examples
Embodiment 1
[0016] Make the polyacrylonitrile precursor pass through two pre-oxidation temperature zones sequentially at a constant speed of 20 m / h in an air medium under normal pressure, and the total time is 45 minutes. The first temperature zone is the cyclization stage, the reaction temperature is 230°C, the air atmosphere, the reaction time is set at 25 minutes, and 3% rigid stretching is added. In the oxidation crosslinking stage of the second temperature zone, the reaction temperature is 265°C, the reaction time is 20 minutes, and 1.5% negative stretching is added. Afterwards, conventional carbonization treatment is carried out under a nitrogen atmosphere for 5 minutes. First, it goes through a low-temperature carbonization process in multiple temperature zones from 300°C to 700°C. At this time, 3% positive drawing is added, and then it is subjected to high-temperature carbonization at about 1300°C. Add 3% negative draft.
[0017] The bulk density and mechanical properties of the ...
Embodiment 2
[0020] Make the polyacrylonitrile precursor pass through three pre-oxidation temperature zones sequentially at a constant speed of 20 m / h in an air medium under normal pressure, and the total time is 33 minutes. The reaction temperature of the cyclization stage in the first temperature zone was 220°C, the reaction time was set at 15 minutes, and 4.5% rigid stretching was added. The second temperature zone is the oxidative cyclization stage, the temperature is 245° C., and the reaction time is set at 6 minutes. The third temperature zone is the cross-linking aromatization stage, the temperature is 270°C, the reaction time is 12 minutes, and 1% negative draft is added. Afterwards, conventional carbonization treatment is carried out under a nitrogen atmosphere for 6 minutes. First, it goes through a low-temperature carbonization process in multiple temperature zones from 300°C to 700°C. At this time, 3% positive drawing is added, and then it is subjected to high-temperature carbo...
Embodiment 3
[0024] Make the polyacrylonitrile precursor pass through four pre-oxidation temperature zones sequentially at a constant speed of 20m / h in an air medium under normal pressure, and the total time is 30 minutes. The reaction temperature in the initial cyclization stage of the first temperature zone was 210°C, the reaction time was set at 9 minutes, and 6% rigid stretching was added. The second temperature zone is the mid-term cyclization stage, the temperature is 230°C, and the reaction time is set at 6 minutes. The third temperature zone is the oxidation cyclization stage, the temperature is 250°C, and the reaction time is 6 minutes. The fourth temperature zone is the cross-linking aromatization stage, the temperature is 270°C, the reaction time is 9 minutes, and 1.5% negative draft is added. Afterwards, conventional carbonization treatment is carried out under a nitrogen atmosphere, and the time is 7 minutes. First, it goes through a low-temperature carbonization process in mu...
PUM
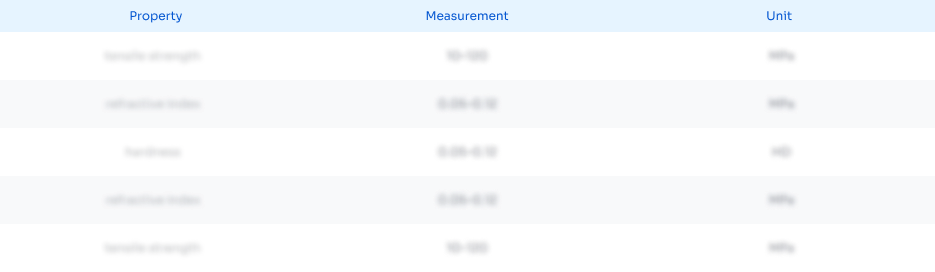
Abstract
Description
Claims
Application Information

- R&D Engineer
- R&D Manager
- IP Professional
- Industry Leading Data Capabilities
- Powerful AI technology
- Patent DNA Extraction
Browse by: Latest US Patents, China's latest patents, Technical Efficacy Thesaurus, Application Domain, Technology Topic, Popular Technical Reports.
© 2024 PatSnap. All rights reserved.Legal|Privacy policy|Modern Slavery Act Transparency Statement|Sitemap|About US| Contact US: help@patsnap.com