Heat-insulating ceramic fiber material and preparation method thereof
A ceramic fiber and thermal insulation material technology, applied in the field of material science, can solve the problems of unsatisfactory application occasions and high thermal conductivity, and achieve the effect of improving thermal insulation performance and simple process
- Summary
- Abstract
- Description
- Claims
- Application Information
AI Technical Summary
Problems solved by technology
Method used
Examples
Embodiment 1
[0020] (1) According to the experimental plan, the molar ratio of ferric nitrate, chromium nitrate and deionized water is 1:1:6 to make a mixed solution in a beaker, and mix evenly to form A liquid;
[0021] (2) Add citric acid to 5 times the molar amount of ethylene glycol to make solution B;
[0022] (3) Slowly add liquid B to liquid A at a ratio of A / B volume ratio of 2, stir evenly, and make liquid C, heat and stir solution C in a water bath at 60°C, and after stirring for 1 hour, a stable the sol;
[0023] (4) Fully impregnate the ceramic fiber in the above sol with a mass ratio of sol / ceramic fiber of 3 for 20 minutes;
[0024] (5) Put the ceramic composite fiber with sol on the surface in an oven, and dry it at 60°C until completely dried;
[0025] (6) Put the composite fiber in a muffle furnace and heat it up to 250°C at 4°C / min, then hold it for 1 hour, then raise the temperature to 600°C at the same rate, hold it for 1 hour, and finally cool it to room temperature ...
Embodiment 2
[0027] (1) According to the experimental plan, the molar ratio of ferric nitrate, chromium nitrate and deionized water is 1:1:8 to make a mixed solution in a beaker, and mix evenly to form A liquid;
[0028] (2) Add citric acid to 6 times the molar amount of ethylene glycol to make solution B;
[0029] (3) Slowly add liquid B to liquid A at a ratio of A / B volume ratio of 3, stir evenly, and make liquid C, heat and stir solution C in a water bath at 60°C, and after stirring for 2 hours, a stable the sol;
[0030] (4) Fully impregnate the ceramic fiber in the above sol with a mass ratio of sol / ceramic fiber of 4 for 25 minutes;
[0031] (5) Put the ceramic composite fiber with sol on the surface in an oven, and dry it at 70°C until completely dried;
[0032] (6) Put the composite fiber in the muffle furnace and heat it up to 250°C at 5°C / min, then keep it warm for 1h, then raise the temperature to 600°C at the same rate, then keep it warm for 1h, and finally cool down to room ...
Embodiment 3
[0034] (1) According to the experimental plan, the molar ratio of ferric nitrate, chromium nitrate and deionized water is 1:1:10 to make a mixed solution in a beaker, and mix evenly to form A liquid;
[0035] (2) Add citric acid to 4 times the molar amount of ethylene glycol to make solution B;
[0036] (3) Slowly add liquid B to liquid A at a ratio of A / B volume ratio of 4, stir evenly, and make liquid C, heat and stir solution C in a water bath at 60°C, and after stirring for 3 hours, a stable the sol;
[0037] (4) Fully impregnate the ceramic fiber in the above sol with a mass ratio of sol / ceramic fiber of 5 for 30 minutes;
[0038] (5) Put the ceramic composite fiber with sol on the surface in an oven, and dry it at 60°C until completely dried;
[0039] (6) Put the composite fiber in a muffle furnace and heat it up to 250°C at 4°C / min, then keep it warm for 1 hour, then raise the temperature to 600°C at the same rate, keep it warm for 1 hour, and finally cool down to roo...
PUM
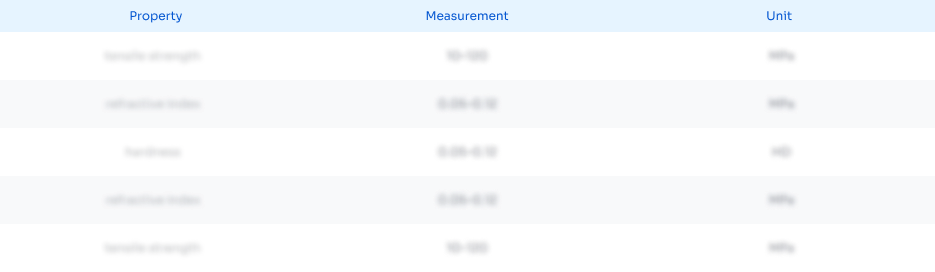
Abstract
Description
Claims
Application Information

- R&D
- Intellectual Property
- Life Sciences
- Materials
- Tech Scout
- Unparalleled Data Quality
- Higher Quality Content
- 60% Fewer Hallucinations
Browse by: Latest US Patents, China's latest patents, Technical Efficacy Thesaurus, Application Domain, Technology Topic, Popular Technical Reports.
© 2025 PatSnap. All rights reserved.Legal|Privacy policy|Modern Slavery Act Transparency Statement|Sitemap|About US| Contact US: help@patsnap.com