Processing method for preparing phosphate rock powder into pellet yellow phosphorus charge
The technology of a mass yellow phosphorus furnace and a processing method is applied in the field of raw material processing and processing of a yellow phosphorus electric furnace, which can solve the problems of easy arching of the furnace, a sharp increase in furnace pressure, and an increase in power consumption, etc. The effect of stable air pressure and low consumption
- Summary
- Abstract
- Description
- Claims
- Application Information
AI Technical Summary
Problems solved by technology
Method used
Examples
Embodiment 1
[0010] Embodiment 1: With the charge cost of 1000kg, the materials are prepared as follows: 1000kg of phosphate rock powder, 100kg of humic acid, and 20kg of sodium hydroxide.
[0011] The preparation method is as follows:
[0012] Step 1: Mix humic acid and sodium hydroxide, add 4 times the weight of water, stir evenly and heat to 95°C, and make a binder for use; Step 2: Put phosphate rock powder into a twin-shaft mixer, add the above Stir the binder evenly; Step 3: Send the above-mentioned uniformly stirred materials to the ball-pressing machine through the screw conveyor to process into pellets of uniform size; Step 4: Send the processed pellets to the pelletizing disc for rolling Polishing; step 5: Send the rolled and polished pellets into the hot air furnace, and preliminarily dry them at 50°C; Step 6: send the preliminarily dried pellets into the vertical kiln at 80°C to 100°C to continue Drying; Step 7: Send the dried pellets to the rotary kiln through a belt conveyor ...
Embodiment 2
[0017] Embodiment 2: With the charge cost of 2000kg, the materials are prepared as follows: 2000kg of phosphate rock powder, 200kg of humic acid, and 40kg of sodium hydroxide.
[0018] The preparation method is as follows:
[0019] Step 1: Mix humic acid and sodium hydroxide, add 4 times the weight of water, stir evenly and heat to 100°C, and make a binder for use; Step 2: Put phosphate rock powder into a twin-shaft mixer, add the above Stir the binder evenly; Step 3: Send the above-mentioned uniformly stirred materials to the ball-pressing machine through the screw conveyor to process into pellets of uniform size; Step 4: Send the processed pellets to the pelletizing disc for rolling Polishing; Step 5: Send the rolled and polished pellets into the hot air furnace for preliminary drying at 55°C; Step 6: Send the preliminarily dried pellets into the vertical kiln at 80°C to 100°C to continue Drying; Step 7: Send the dried pellets to the rotary kiln through a belt conveyor for ...
Embodiment 3
[0024] Embodiment 3: With the charge cost of 3000kg, the materials are prepared as follows: 3000kg of phosphate rock powder, 300kg of humic acid, and 60kg of sodium hydroxide.
[0025] The preparation method is as follows:
[0026] Step 1: Mix humic acid and sodium hydroxide, add 4 times the weight of water, stir evenly and heat to 98°C, and make a binder for use; Step 2: Put phosphate rock powder into a twin-shaft mixer, add the above Stir the binder evenly; Step 3: Send the above-mentioned uniformly stirred materials to the ball-pressing machine through the screw conveyor to process into pellets of uniform size; Step 4: Send the processed pellets to the pelletizing disc for rolling Polishing; Step 5: Send the rolled and polished pellets into the hot air furnace for preliminary drying at 60°C; Step 6: Send the preliminarily dried pellets into the vertical kiln at 80°C to 100°C to continue Drying; Step 7: Send the dried pellets to the rotary kiln through a belt conveyor for c...
PUM
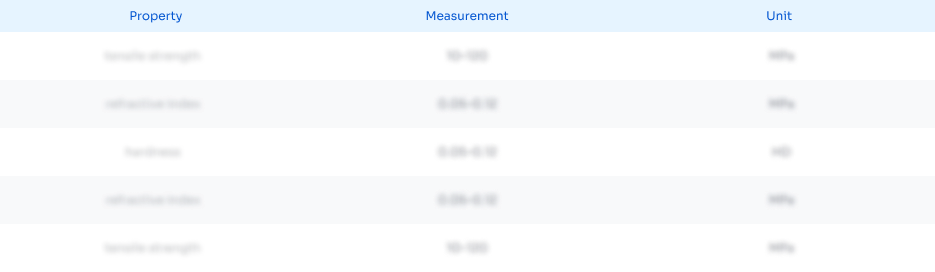
Abstract
Description
Claims
Application Information

- R&D
- Intellectual Property
- Life Sciences
- Materials
- Tech Scout
- Unparalleled Data Quality
- Higher Quality Content
- 60% Fewer Hallucinations
Browse by: Latest US Patents, China's latest patents, Technical Efficacy Thesaurus, Application Domain, Technology Topic, Popular Technical Reports.
© 2025 PatSnap. All rights reserved.Legal|Privacy policy|Modern Slavery Act Transparency Statement|Sitemap|About US| Contact US: help@patsnap.com