Calcium plastic corrugated board and production method thereof
A technology of corrugated board and calcium plastic, which is applied in the field of packaging materials, can solve the problems of high cost, achieve comprehensive performance improvement, good performance, and increase the effect of breaking force
- Summary
- Abstract
- Description
- Claims
- Application Information
AI Technical Summary
Problems solved by technology
Method used
Image
Examples
preparation example Construction
[0015] (1) Preparation of modified calcium carbonate:
[0016] Ingredients in proportion: heavy calcium carbonate 42%, light calcium carbonate 50%, talcum powder 6%, chlorinated paraffin 2%, put the weighed formula component raw materials into a high-speed mixer, stir at a temperature of 55°C for 15 Minutes, obtain modified calcium carbonate;
[0017] (2) Weigh the materials according to the proportion, knead and stir the weighed raw materials, control the temperature at 95-105°C, and knead in the kneader for 5-8 minutes;
[0018] (3) Mixing and plasticizing: the kneaded mixture enters the internal mixer, at a temperature of 180°-205°C, mechanically pressurizes 35-45Mpa, and plasticizes for 7 minutes;
[0019] (4) Open refining and plasticizing: the mixed material after banbury mixing enters the open mixer, at a temperature of 180°-205°C, mechanically presses 35-45Mpa, and plasticizes for 10 minutes; then enters the rolling and plasticizing process;
[0020] (4) Rolling and ...
Embodiment
[0026] 1. Prepare modified calcium carbonate first: weigh 12.5kg of light calcium carbonate, 10.5kg of heavy calcium carbonate, 1.5kg of talcum powder, and 0.5kg of chlorinated paraffin, add them to a high-speed mixer, and fully stir the reaction at 55°C , the stirring time is 10-15 minutes to obtain modified calcium carbonate;
[0027] 2. Weigh 0.5kg of stearic acid, 0.4kg of titanium dioxide, 0.1kg of ultramarine blue, 0.1kg of whitening agent and mix well, mix with 25kg of modified calcium carbonate, 3.5kg of high-density polyethylene, 3.5kg of low-density polyethylene, 1.5kg of high-strength polyethylene provided by Changshu Xiubo Fiber Co., Ltd., 25kg of calcium-plastic recycled materials, about 60kg in total, poured into the kneader, the temperature was controlled at 105°C, kneaded at high speed for 7 minutes, and the material was transferred to the internal mixer. At a temperature of 200°C, apply a mechanical pressure of 40Mpa, banbury and plasticize for 7 minutes, tran...
PUM
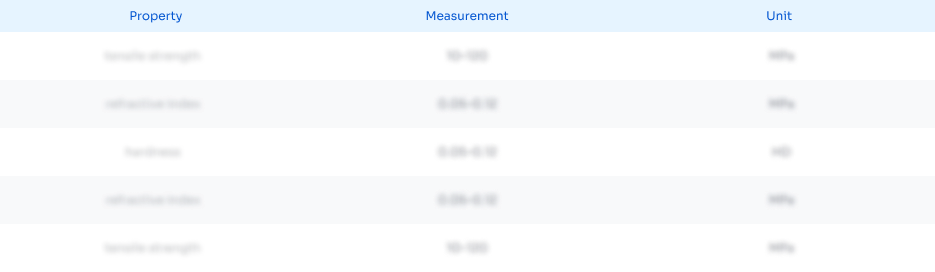
Abstract
Description
Claims
Application Information

- R&D Engineer
- R&D Manager
- IP Professional
- Industry Leading Data Capabilities
- Powerful AI technology
- Patent DNA Extraction
Browse by: Latest US Patents, China's latest patents, Technical Efficacy Thesaurus, Application Domain, Technology Topic, Popular Technical Reports.
© 2024 PatSnap. All rights reserved.Legal|Privacy policy|Modern Slavery Act Transparency Statement|Sitemap|About US| Contact US: help@patsnap.com