Production line for fireproof heat-insulating wall plates, and method for on-site processing of fireproof heat-insulating wall plates by utilizing production line
A technology of fire prevention, heat preservation and on-site processing, which is applied in the direction of manufacturing tools, ceramic molding workshops, ceramic molding machines, etc., which can solve the problems of bulky elevators, poor economic benefits, and large investment, and achieve transportation cost savings, simple equipment, and low investment. Effect
- Summary
- Abstract
- Description
- Claims
- Application Information
AI Technical Summary
Problems solved by technology
Method used
Image
Examples
Embodiment 1
[0034] Embodiment one: if Figure 1-2 As shown, the production line of this fireproof and thermal insulation wallboard includes a mixer 1, a pouring vehicle 2 and two columns of casting molds 3, the mixer 1 includes a stirring tank 101, and the stirring tank 101 is internally provided with a stirring paddle driven by an external motor, and the stirring tank 101 The top is equipped with a liquid feeding device and a solid feeding device, and the bottom of the stirring tank 101 is provided with a discharge valve 102, and the stirring tank 101 is fixed on a support 113, and the support is provided with four legs, and the four legs support the stirring tank 101 , forming a passing space 103 .
[0035] Described liquid feeding device comprises water storage tank 104, and this water storage tank 104 is provided with liquid level gauge 105, and its bottom communicates with stirring tank 101 through discharge pipe, and this discharge pipe is provided with valve 106; The solid The fee...
Embodiment 2
[0047] Embodiment 2: In step 1 of processing the fire-proof and thermal insulation wallboard: 50 parts by weight of high-strength concrete, 32 parts by weight of sawdust, straw or other plant fiber powder, 40 parts by weight of fly ash, 48 parts by weight of water Put it into the mixing tank and stir for 2.5 minutes to get the pouring slurry; in the ③ step: indoor curing is 3.5 hours, indoor curing is 5 days, outdoor natural curing time is 18 days, and the remaining steps and operations are as shown in Example 1 .
Embodiment 3
[0048] Embodiment three: process the fire-proof thermal insulation wall board in step ①: the high-strength concrete of 55 parts by weight, the sawdust of 35 parts by weight, orange stalk or other plant fiber powder, the fly ash of 40 parts by weight, the water of 40 parts by weight Put it into the mixing tank and stir for 2-3 minutes to get the pouring slurry; in the 3rd step: indoor curing is 4.5 hours, indoor curing is 4 days, outdoor natural curing time is 20 days, and the remaining steps and operations are as in Example 1 shown.
[0049] The cement foam insulation board used in the above embodiment is made according to the following method:
[0050] The first manufacturing method of the cement foam insulation board:
[0051] ⑴. Get the 525 cement of 50 parts by weight, the fly ash of 36 parts by weight, the calcium hardate (national standard) of 1.3 parts by weight and the sodium hexametaphosphate (national standard) of 0.4 parts by weight, drop into described agitator t...
PUM
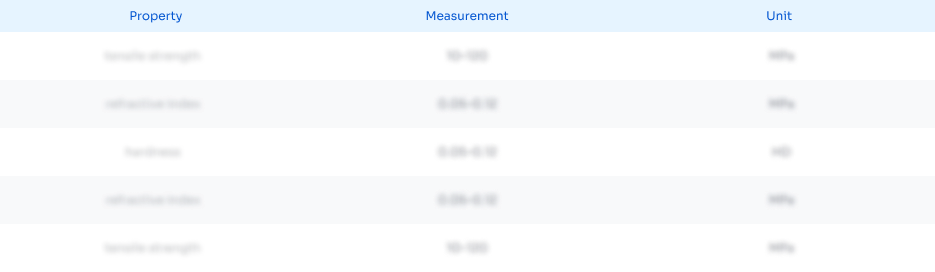
Abstract
Description
Claims
Application Information

- R&D
- Intellectual Property
- Life Sciences
- Materials
- Tech Scout
- Unparalleled Data Quality
- Higher Quality Content
- 60% Fewer Hallucinations
Browse by: Latest US Patents, China's latest patents, Technical Efficacy Thesaurus, Application Domain, Technology Topic, Popular Technical Reports.
© 2025 PatSnap. All rights reserved.Legal|Privacy policy|Modern Slavery Act Transparency Statement|Sitemap|About US| Contact US: help@patsnap.com