Wire drawing film coating machine
A coating machine and wire drawing technology, which is applied to the device and coating of the surface coating liquid, can solve the problems of inability to guarantee the quality of the drawing film, the coating accuracy is not accurate enough, and the quality of the drawing film is affected.
- Summary
- Abstract
- Description
- Claims
- Application Information
AI Technical Summary
Problems solved by technology
Method used
Image
Examples
Embodiment 1
[0036] A wire drawing film coating machine, comprising a controller, the controller is electrically connected to a coiling unit 1, a conveying unit 2, a coating unit 3, a drying device 4 and a winding unit 5 in sequence, and the coiling unit 1 includes a winding unit The unwinding machine base is provided with an unwinding air shaft 10 and a flattening roller for fixing the unwinding film roll on the unwinding machine base, and the flattening roller is located between the unwinding air shaft 10 and the conveying unit 2 , A deviation correcting device 13 is provided between the flattening roller and the conveying unit 2 .
[0037] Specifically, the film roll to be coated is passed into the unwinding air shaft 10, and then inflated by the inflation device, the unwinding air shaft 10 can be closely attached to the film roll, and no slippage will occur during the coating process Phenomenon, to ensure the accuracy of coating. The flattening roller is used to flatten and transport ...
Embodiment 2
[0045] The difference between this embodiment and Embodiment 1 is: the bottom of the trough 32 is provided with a feeding port, and the feeding port is connected with a feeding device, and the feeding device includes a feeding pipe, a paint storage device 38 and a transmission power mechanism Specifically, the transmission power mechanism is a delivery pump 39 , the paint storage device 38 is connected to the delivery pump 39 , and the paint is delivered to the material tank 32 through the delivery pump 39 . The prepared paint is placed in the paint storage device 38, and then the paint is delivered to the material tank 32 by the delivery pump 39. The liquid level of the paint in the material tank 32 can be adjusted at any time, and the remaining paint can be stored in the paint storage device 38 again. In the process, prevent the paint from being in contact with the air for too long and affect the quality of the paint.
[0046] The drying device 4 includes 4 drying sections....
Embodiment 3
[0052] The difference between this embodiment and the second embodiment is that: the winding unit 5 further includes a tracking and positioning device 53 located between the winding air shaft 52 and the tension control device 55 . The tracking and positioning device 53 controls the tightness of the film material during winding.
[0053] The tracking and positioning device 53 includes a tracking roller set and a sliding mechanism. The tracking roller set includes a fixed seat on which a rubber pressing roller and a passing roller are mounted, and the fixed seat is slidably connected to the sliding mechanism. The sliding mechanism is set on the unwinding base, and is equipped with a slide rail. The tracking roller group is provided with a rubber roller and a roller through the fixed seat. The film passes through the roller to reach the rubber roller and then to the winding air shaft 52. When the film material is in the process of continuous winding, the rubber roller will be clo...
PUM
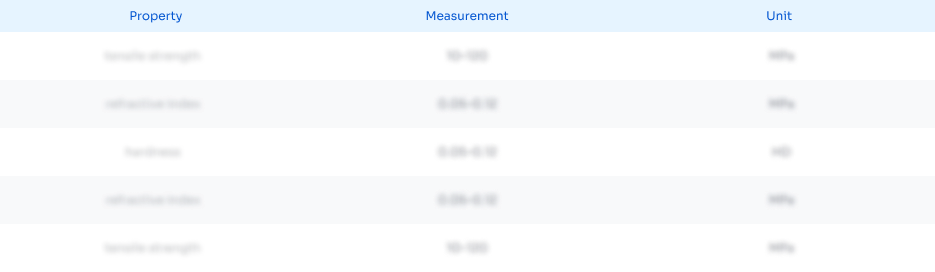
Abstract
Description
Claims
Application Information

- R&D Engineer
- R&D Manager
- IP Professional
- Industry Leading Data Capabilities
- Powerful AI technology
- Patent DNA Extraction
Browse by: Latest US Patents, China's latest patents, Technical Efficacy Thesaurus, Application Domain, Technology Topic, Popular Technical Reports.
© 2024 PatSnap. All rights reserved.Legal|Privacy policy|Modern Slavery Act Transparency Statement|Sitemap|About US| Contact US: help@patsnap.com