Fiber optic gyroscope eight-position calibration method based on rotating mechanism
A fiber optic gyroscope and a calibration method technology, applied in the field of measurement, can solve the problems of no longer satisfying high-precision fiber optic gyroscope components, rate error calibration parameter coupling error of large indexing mechanism, etc.
- Summary
- Abstract
- Description
- Claims
- Application Information
AI Technical Summary
Problems solved by technology
Method used
Image
Examples
Embodiment Construction
[0068] The specific embodiment of the present invention is described in detail below in conjunction with accompanying drawing:
[0069] (1) Fasten the fiber optic gyro assembly to the table of the biaxial indexing mechanism, and level the table and side of the indexing mechanism to ensure that the coordinate system of the gyroscope coincides with the coordinate system of the indexing mechanism, and adjust the indexing before the experiment starts mechanism so that it is parallel to the local water level;
[0070] (2) Utilize the global positioning system GPS to determine the initial position parameters of the carrier, and bind them into the navigation computer;
[0071] (3) The strapdown inertial navigation system is preheated, and the data output by the fiber optic gyroscope and the quartz accelerometer are collected and processed;
[0072] (4) Establish a simple error model of the fiber optic gyroscope;
[0073] Different from the mechanical gyroscope, the optical fiber gy...
PUM
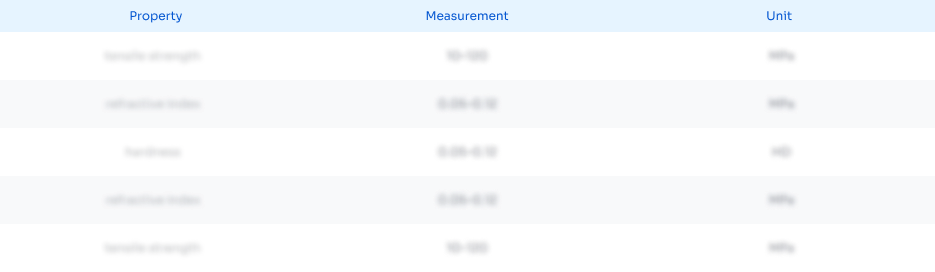
Abstract
Description
Claims
Application Information

- R&D Engineer
- R&D Manager
- IP Professional
- Industry Leading Data Capabilities
- Powerful AI technology
- Patent DNA Extraction
Browse by: Latest US Patents, China's latest patents, Technical Efficacy Thesaurus, Application Domain, Technology Topic, Popular Technical Reports.
© 2024 PatSnap. All rights reserved.Legal|Privacy policy|Modern Slavery Act Transparency Statement|Sitemap|About US| Contact US: help@patsnap.com