Designing method for cross wedge rolling mould of conical surface stepped shaft part
A technology of die design and step shaft, which is used in metal extrusion forming tools, manufacturing tools, metal processing equipment, etc., can solve problems such as large amount of calculation, difficulty in guaranteeing the accuracy of truncation curves and rolling curves, and inconvenient die design. , to achieve the effect of simplifying design and manufacturing
- Summary
- Abstract
- Description
- Claims
- Application Information
AI Technical Summary
Problems solved by technology
Method used
Image
Examples
Embodiment
[0104] Using finite element technology to simulate the process of double forming surface method and traditional cross wedge rolling forming tapered step shaft parts respectively in the computer. The parameters of the shaft parts are as follows: the inclination angle of the conical surface step α 1 =70°, the minimum radius r of the conical step shaft 0 =8.2mm, the maximum radius r of conical stepped shaft parts 1 =15mm, widening angle β=8°, half length L of final widening 1 =18mm.
[0105] refer to figure 1 with figure 2 , it can be seen from the figure that the equivalent stress at point P inside the cross-wedge rolling part is smaller than that of the traditional cross-wedge rolling technology before the forming is stable.
[0106] refer to Figure 11 , apply the above-mentioned mold design method to design the mold for the conical step shaft parts. The parameters shown in the figure below take α=30°, α 1 =40°, β=8°, r 1 =16mm, r 0 =8.1mm, l=17.5mm forgings for die...
PUM
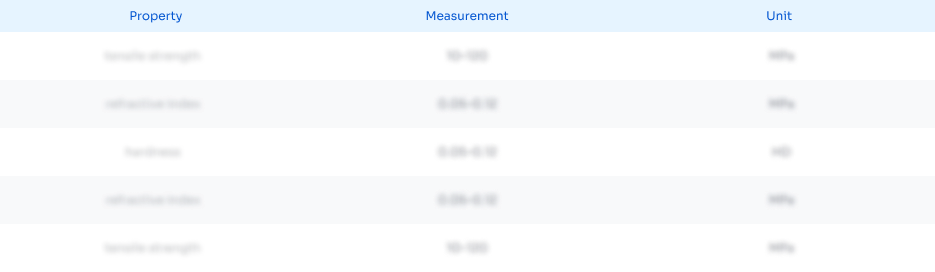
Abstract
Description
Claims
Application Information

- R&D
- Intellectual Property
- Life Sciences
- Materials
- Tech Scout
- Unparalleled Data Quality
- Higher Quality Content
- 60% Fewer Hallucinations
Browse by: Latest US Patents, China's latest patents, Technical Efficacy Thesaurus, Application Domain, Technology Topic, Popular Technical Reports.
© 2025 PatSnap. All rights reserved.Legal|Privacy policy|Modern Slavery Act Transparency Statement|Sitemap|About US| Contact US: help@patsnap.com