High color fastness cotton fabric dyeing method capable of effectively saving water and reducing pollution
A technology of high color fastness and dyeing method, applied in the field of textile printing and dyeing, can solve the problems of low dyeing rate and color fixing rate, easy hydrolysis of reactive dyes, low utilization rate of dyes, etc., to save dye consumption and improve rubbing resistance. Fastness and color fastness to washing, the effect of improving wearability
- Summary
- Abstract
- Description
- Claims
- Application Information
AI Technical Summary
Problems solved by technology
Method used
Examples
preparation example Construction
[0072] The preparation of feather protein powder specifically implements according to the following steps:
[0073] 1) Pre-treatment of chicken feathers:
[0074] Collect the chicken feathers and wash the chicken feathers with tap water first;
[0075] Weigh glacial acetic acid and dissolve glacial acetic acid in water to prepare an acetic acid solution with a concentration of 0.3% to 0.7% by volume. Put the cleaned chicken feathers into the prepared acetic acid solution at a temperature of 30°C to 50°C Pretreatment is carried out in the middle, the chicken feather quality and the acetic acid solution quality are ratio 1: 30~50, and the pretreatment time is 5min~15min;
[0076] After the pre-treatment of the chicken feathers is completed, the chicken feathers are fished out, and the chicken feathers are washed with tap water again until the cleaning solution shows that the pH value is neutral;
[0077] Dry the chicken feathers after cleaning at normal temperature;
[0078] ...
Embodiment 1
[0123] Collect the chicken feathers and clean them, configure an acetic acid solution with a concentration of 0.3% by volume, pour the clean chicken feathers into the acetic acid solution at 30°C, the mass ratio of the chicken feathers to the acetic acid solution is 1:30, pre-treat for 5 minutes; use tap water Clean the chicken feathers, dry the cleaned chicken feathers at room temperature; configure 3g / L sodium bisulfite solution as a pretreatment solution, heat the pretreatment solution at a temperature of 50°C, and put the dried chicken feathers into the pretreatment solution In this method, the mass ratio of chicken feathers to the pretreatment solution is 1:10, and the pretreatment time is 10 minutes; the chicken feather protein solution is prepared according to the quality of the pretreated chicken feathers, and the mass ratio of chicken feathers to the solution is 1:10. Dissolve urea and sodium hydroxide in water to form a feather protein solution. The mass ratio of urea...
Embodiment 2
[0132] Collect the chicken feathers and clean them, prepare an acetic acid solution with a concentration of 0.5% by volume, pour the clean chicken feathers into the acetic acid solution at 40°C, the mass ratio of the chicken feathers to the acetic acid solution is 1:40, pre-treat for 10 minutes; use tap water Clean the chicken feathers, dry the cleaned chicken feathers at room temperature; configure 7g / L sodium bisulfite solution as a pretreatment solution, heat the pretreatment solution at 70°C, and put the dried chicken feathers into the pretreatment solution In this method, the mass ratio of chicken feathers to the pretreatment solution is 1:20, and the pretreatment time is 15 minutes; the chicken feather protein solution is prepared according to the quality of the pretreated chicken feathers, and the mass ratio of chicken feathers to the solution is 1:20. Dissolve urea and sodium hydroxide in water to form a feather protein solution. The mass ratio of urea and sodium hydrox...
PUM
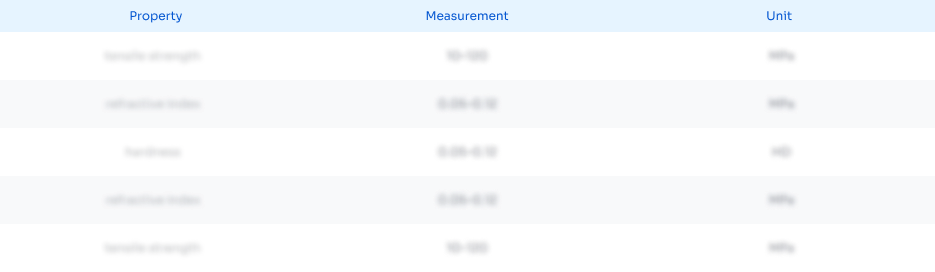
Abstract
Description
Claims
Application Information

- R&D
- Intellectual Property
- Life Sciences
- Materials
- Tech Scout
- Unparalleled Data Quality
- Higher Quality Content
- 60% Fewer Hallucinations
Browse by: Latest US Patents, China's latest patents, Technical Efficacy Thesaurus, Application Domain, Technology Topic, Popular Technical Reports.
© 2025 PatSnap. All rights reserved.Legal|Privacy policy|Modern Slavery Act Transparency Statement|Sitemap|About US| Contact US: help@patsnap.com