Method for manufacturing telescopic shaft and telescopic shaft manufactured by same
A manufacturing method and telescopic shaft technology, which is applied to steering control, couplings, steering control, etc. installed on the vehicle, and can solve the problems of sliding resistance fluctuations, high torque of the intermediate shaft 16, difficulty for lubricating oil to reach the pressing concave surface 611, etc. question
- Summary
- Abstract
- Description
- Claims
- Application Information
AI Technical Summary
Problems solved by technology
Method used
Image
Examples
Embodiment 1
[0048] Hereinafter, embodiments of the present invention will be described based on the drawings. figure 1 It is a side view showing the whole steering device having a telescoping shaft according to the present invention with a part cut away, showing an embodiment applicable to an electric power steering device having a control auxiliary part. figure 2 It is a longitudinal cross-sectional view showing the manufacturing process of the telescopic shaft according to the first embodiment of the present invention. image 3 express figure 2 The enlarged cross-sectional view of image 3 (a) is an enlarged sectional view showing a telescoping shaft covered with a sleeve, image 3 (b) is an enlarged cross-sectional view showing the telescopic shaft of the coated portion.
[0049] Figure 4 It is a perspective view showing the male shaft of the telescopic shaft in Embodiment 1 of the present invention, Figure 5 It shows the manufacturing process of the telescopic shaft of Examp...
Embodiment 2
[0086] Next, Example 2 of the present invention will be described. Figure 10 It is an enlarged cross-sectional view showing the telescopic shaft of Embodiment 2 of the present invention, which is the same as that of Embodiment 1. image 3 (b) equivalent graph, Figure 11 yes Figure 10 The enlarged cross-sectional view of the R portion, which is the same as that of Example 1 Figure 5 (b) equivalent graph, Figure 12 yes Figure 11 The enlarged cross-sectional view of part S of . In the following description, only structural parts different from those of the above-mentioned embodiments will be described, and repeated descriptions will be omitted. In addition, the same symbols are attached to the same members and will be described. Example 2 is an example in which the covering portion 61 is bonded to the tooth surface of the protruding bar tooth 51 with an adhesive.
[0087] That is, if Figure 10 to Figure 12 As shown, for the telescopic shaft of Example 2, the female...
Embodiment 3
[0098] Next, Example 3 of the present invention will be described. Figure 13 It is an enlarged cross-sectional view of the meshing portion of the telescopic shaft according to the third embodiment of the present invention. In the following description, only structural parts different from those of the above-mentioned embodiments will be described, and repeated descriptions will be omitted. In addition, the same symbols are attached to the same members and will be described. Embodiment 3 is an example in which a wedge-shaped gap is formed at the meshing portion between the tooth surface of the protruding rack tooth 51 and the tooth surface of the tooth groove 41 toward both ends in the tooth height direction.
[0099] That is, if Figure 13 As shown, for the telescopic shaft of Embodiment 3, the convex tooth 51 of the male shaft 16A is covered with a material that reduces the sliding resistance between the convex tooth 51 and the tooth groove 41 of the female shaft (female s...
PUM
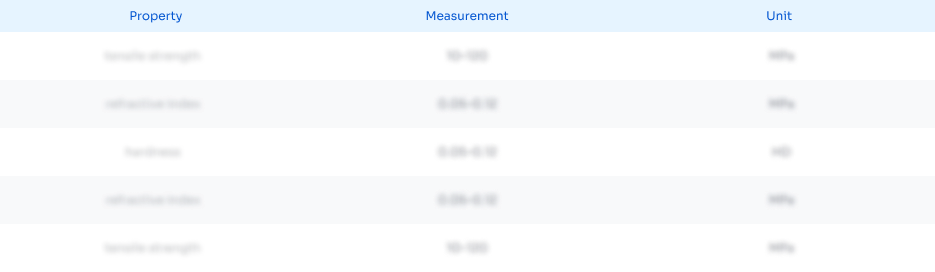
Abstract
Description
Claims
Application Information

- Generate Ideas
- Intellectual Property
- Life Sciences
- Materials
- Tech Scout
- Unparalleled Data Quality
- Higher Quality Content
- 60% Fewer Hallucinations
Browse by: Latest US Patents, China's latest patents, Technical Efficacy Thesaurus, Application Domain, Technology Topic, Popular Technical Reports.
© 2025 PatSnap. All rights reserved.Legal|Privacy policy|Modern Slavery Act Transparency Statement|Sitemap|About US| Contact US: help@patsnap.com