High-purity manganese metal and preparation method thereof
A manganese metal, purity technology, applied in the direction of improvement of process efficiency, photographic technology, instruments, etc., can solve the problems of inability to wash and recycle slag, high consumption of sulfuric acid, low resource utilization rate, etc., to improve the utilization rate of manganese resources, improve the overall Manganese recovery rate and production cost reduction effect
- Summary
- Abstract
- Description
- Claims
- Application Information
AI Technical Summary
Problems solved by technology
Method used
Image
Examples
preparation example Construction
[0034] The present invention provides a method for preparing metal manganese with a purity of 99.99wt% or more. The method includes: a first step, mixing manganese sulfate solution with a concentration of 100-350g / L, preferably 250-300g / L, and NH 3 Gas and H 2 S gas carries out vulcanization reaction, and the pH value of the reaction solution during the vulcanization reaction is controlled within the range of 5.5-6.5 (preferably 5.71-6.24); in the second step, [Mn 2+ ] <200ppm, stop the vulcanization reaction, and then separate the solid and liquid to obtain the filter cake; the third step is to wash the filter cake, acidify the solution with sulfuric acid, and separate the solid and liquid to obtain the filtrate; the fourth step is to obtain the filtrate The filtrate is electrolyzed to obtain metal manganese.
[0035] The invention provides manganese metal with a purity of more than 99.99wt%. The content of Ca in the manganese metal is less than or equal to 0.0013%, and the ...
Embodiment 1
[0044] The flue gas uses industrial-grade barium carbonate carbon to reduce the exhaust gas of the rotary kiln, with an average gas volume of 25000Nm 3 / h, average SO 2 Content 13400mg / m 3 , The outlet temperature of the cyclone dust collector is about 170°C. Medium and low grade MnO 2 Mineral powder (15% by weight containing Mn) is beaten with the filtrate after washing with sulfurized reactants to obtain slurry, and then passed through sulfur-containing flue gas for reaction to generate manganese sulfate solution, and then adjust its concentration to 250g / L.
[0045] Add the manganese sulfate solution with a concentration of 250g / L into the third stage of the three-stage vulcanization device. Introduce NH in the first stage of the three-stage vulcanization unit 3 Gas and H 2 Mixed gas of S gas, NH 3 Gas and H 2 The molar ratio of S gas is 2:1. The gas velocity of the mixed gas in each stage of vulcanization device is controlled at 2m / sec, and the average flow rate ...
Embodiment 2
[0051] The flue gas uses industrial-grade barium carbonate carbon to reduce the exhaust gas of the rotary kiln, with an average gas volume of 25000Nm 3 / h, average SO 2 Content 13400mg / m 3 , The outlet temperature of the cyclone dust collector is about 170°C. Medium and low grade MnO 2 Mineral powder (containing Mn is 20% (by weight)) is beaten with the filtrate after washing with sulfurized reactants to obtain slurry, and then passed through sulfur-containing flue gas for reaction to generate manganese sulfate solution, and then adjust its concentration to 300g / L.
[0052] Add the manganese sulfate solution with a concentration of 300g / L into the third stage of the three-stage vulcanization device. Introduce NH in the first stage of the three-stage vulcanization unit 3 Gas and H 2 Mixed gas of S gas, NH 3 Gas and H 2 The molar ratio of S gas is 2:1. The gas velocity of the mixed gas in each stage of vulcanization device is controlled at 2m / sec, and the average flow ...
PUM
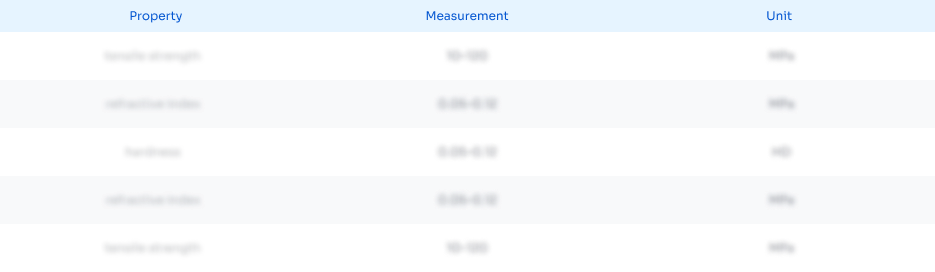
Abstract
Description
Claims
Application Information

- R&D
- Intellectual Property
- Life Sciences
- Materials
- Tech Scout
- Unparalleled Data Quality
- Higher Quality Content
- 60% Fewer Hallucinations
Browse by: Latest US Patents, China's latest patents, Technical Efficacy Thesaurus, Application Domain, Technology Topic, Popular Technical Reports.
© 2025 PatSnap. All rights reserved.Legal|Privacy policy|Modern Slavery Act Transparency Statement|Sitemap|About US| Contact US: help@patsnap.com