Method and device for preparing basic magnesium carbonate from heavy magnesium carbonate water by pyrolysis
A technology of magnesium carbonate and heavy magnesium water, which is applied in the direction of magnesium carbonate, can solve the problems of low heat energy utilization rate, short operation cycle, and high heat loss, and achieve high heat energy utilization rate, obvious energy saving effect, and low fuel consumption.
- Summary
- Abstract
- Description
- Claims
- Application Information
AI Technical Summary
Problems solved by technology
Method used
Image
Examples
Embodiment 1
[0034] A kind of pyrolysis heavy magnesium water produces the method (as figure 1 shown), which includes the following steps:
[0035] The temperature is 20°C, the mass concentration is 100g / L magnesium bicarbonate aqueous solution and the temperature is 40°C saturated basic magnesium carbonate solution, the volume ratio is 1:29 (the flow rate of magnesium bicarbonate aqueous solution is 2m 3 / h, the flow rate of saturated basic magnesium carbonate solution is 58m 3 / h) After mixing, enter the pyrolyzer with a temperature of 40°C for heat exchange, and the residence time is 240min. Liquid separation, solid-liquid separation to obtain solid basic magnesium carbonate crystals, solid basic magnesium carbonate crystals were dried at 180°C for 3 hours (110.6kg / h); the saturated basic magnesium carbonate solution at a temperature of 40°C came from centrifugal sedimentation The resulting light phase.
[0036] Realize described pyrolysis heavy magnesium water to produce the device ...
Embodiment 2
[0039] A method for pyrolyzing heavy magnesium water to produce basic magnesium carbonate, comprising the steps of:
[0040] The temperature is 30°C, the mass concentration is 12g / L magnesium bicarbonate aqueous solution and the temperature is 90°C saturated basic magnesium carbonate solution at a volume ratio of 1:2 (the flow rate of magnesium bicarbonate aqueous solution is 20m 3 / h, the flow rate of saturated basic magnesium carbonate solution is 40m 3 / h) After mixing, enter the pyrolyzer with a temperature of 90°C for heat exchange, and the residence time is 10min. After the heat exchange, the reaction liquid is separated from solid and liquid to obtain solid basic magnesium carbonate crystals and filtrate, and part of the filtrate is refluxed with bicarbonate The magnesium aqueous solution is mixed, and the other part is sent to the post-treatment process. The obtained solid basic magnesium carbonate crystals are dried at 200°C for 2.5 hours (132.7kg / h). That is to say,...
Embodiment 3
[0044] A method for pyrolyzing heavy magnesium water to produce basic magnesium carbonate, comprising the steps of:
[0045] The temperature is 60°C, the mass concentration is 20g / L magnesium bicarbonate aqueous solution and the temperature is 70°C and the saturated basic magnesium carbonate solution containing a small amount of solid crystals has a volume ratio of 1:0.05 (the flow rate of the magnesium bicarbonate aqueous solution is 10m 3 / h, the flow rate of saturated basic magnesium carbonate solution is 0.5m 3 / h) After mixing, enter the pyrolyzer with a temperature of 70°C to exchange heat, and the residence time is 40min. After the heat exchange, part of the reaction liquid is refluxed and mixed with an aqueous solution of magnesium bicarbonate, and the other part is separated into solid and liquid to obtain solid basic carbonic acid Magnesium crystals, solid basic magnesium carbonate crystals are obtained by drying at 220°C for 2 hours (110.6kg / h). That is to say, the...
PUM
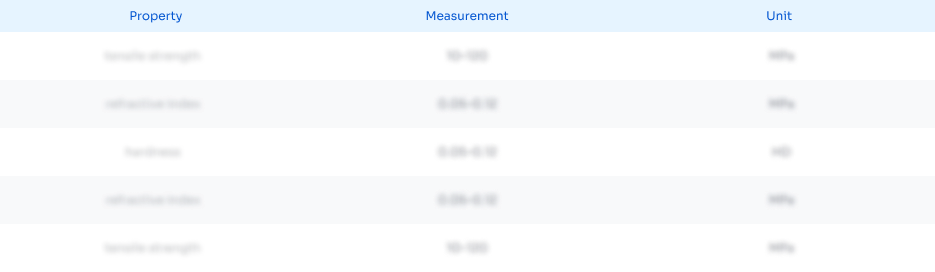
Abstract
Description
Claims
Application Information

- Generate Ideas
- Intellectual Property
- Life Sciences
- Materials
- Tech Scout
- Unparalleled Data Quality
- Higher Quality Content
- 60% Fewer Hallucinations
Browse by: Latest US Patents, China's latest patents, Technical Efficacy Thesaurus, Application Domain, Technology Topic, Popular Technical Reports.
© 2025 PatSnap. All rights reserved.Legal|Privacy policy|Modern Slavery Act Transparency Statement|Sitemap|About US| Contact US: help@patsnap.com