Brake tester with combination of mechanical analogue and electric inertia analogue and control algorithm
A technology of mechanical simulation and simulation control, which is applied in the testing of mechanical components, testing of machine/structural components, instruments, etc., and can solve the problems of not being able to meet the test rhythm, increasing the number of bearings, and not always being able to accurately match
- Summary
- Abstract
- Description
- Claims
- Application Information
AI Technical Summary
Problems solved by technology
Method used
Image
Examples
Embodiment Construction
[0044] like figure 1 As shown, the brake test bench with the combination of mechanical simulation and electric inertia simulation includes at least a speed sensor 1 , a drive motor 2 , a torque sensor 3 , a flywheel 4 , an electric transmission control unit 5 and an electric inertia simulation control unit 6 . A torque sensor 3 is installed between the drag motor 2 and the flywheel group 4, and a speed sensor 1 is installed at the end of the shaft. The motor 2 drives the flywheel or the flywheel group 4 to run to the set speed, and starts the braking process; the flywheel speed and motor output torque synchronously collected by the torque sensor 3 and the speed sensor 1 are obtained by the electric inertia simulation control unit 6, and the electric inertia simulation control Unit 6 calculates the total drop value of the flywheel kinetic energy relative to the given initial speed of the test, calculates the total energy that the motor should compensate based on the mathematica...
PUM
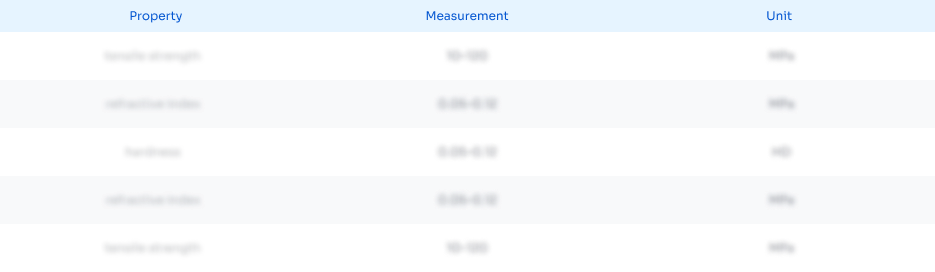
Abstract
Description
Claims
Application Information

- R&D
- Intellectual Property
- Life Sciences
- Materials
- Tech Scout
- Unparalleled Data Quality
- Higher Quality Content
- 60% Fewer Hallucinations
Browse by: Latest US Patents, China's latest patents, Technical Efficacy Thesaurus, Application Domain, Technology Topic, Popular Technical Reports.
© 2025 PatSnap. All rights reserved.Legal|Privacy policy|Modern Slavery Act Transparency Statement|Sitemap|About US| Contact US: help@patsnap.com