Vibration damping system with steering automatic balance
A shock absorption system and balancing technology, applied in the interconnection system, suspension, transportation and packaging, etc., can solve problems such as complex structure, difficult implementation and maintenance, etc., achieve vibration reduction, reduce the inclination of the suspension car body, and facilitate adjustment Effect
- Summary
- Abstract
- Description
- Claims
- Application Information
AI Technical Summary
Problems solved by technology
Method used
Image
Examples
Embodiment Construction
[0013] The damping system with steering balance of the present invention includes four damper combination mechanisms corresponding to four wheels. Each combined mechanism includes three or more shock absorbers or a combination of shock absorbers and rigid metal rods. Shock absorbers or rigid metal rods, connected in a star (Y-shape), delta (delta-shape) or a combination of star and delta configurations. It is characterized in that the shock absorbers are connected head to head or end to end or end to end. A joint-like rotatable connection. Specifically: the shock absorber or rigid metal rod 1 is a common spring shock absorber or hydraulic shock absorber or air shock absorber or a rigid metal frame, and only one end of A in the shock absorber or rigid metal rod 1 is rotatable Connected to the axle 6, the other end is rotatably connected to one end of another shock absorber B and C, and the other end of B in the shock absorber or rigid metal rod 1 is rotatably connected to the...
PUM
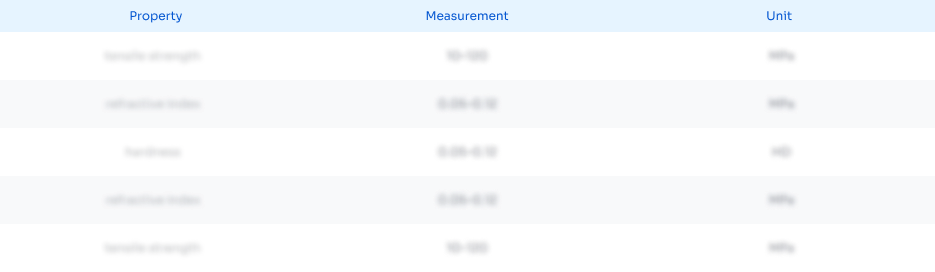
Abstract
Description
Claims
Application Information

- Generate Ideas
- Intellectual Property
- Life Sciences
- Materials
- Tech Scout
- Unparalleled Data Quality
- Higher Quality Content
- 60% Fewer Hallucinations
Browse by: Latest US Patents, China's latest patents, Technical Efficacy Thesaurus, Application Domain, Technology Topic, Popular Technical Reports.
© 2025 PatSnap. All rights reserved.Legal|Privacy policy|Modern Slavery Act Transparency Statement|Sitemap|About US| Contact US: help@patsnap.com