Method for transforming wolframite into scheelite
A technology of wolframite and scheelite, applied in the direction of improving process efficiency, etc., can solve the problems of economical and effective separation of precipitation, generation of acid-base waste liquid, pollution of the environment, etc., to increase surface area, improve decomposition rate, improve The effect of economic benefits
- Summary
- Abstract
- Description
- Claims
- Application Information
AI Technical Summary
Problems solved by technology
Method used
Examples
Embodiment 1
[0033] In a muffle furnace, add WO to 500 g 3 65% by weight of wolframite concentrate with a particle size of -320 mesh was added with 1.2 times the theoretical amount (ie, 168 g) of calcium carbonate, the reaction temperature was 1000 degrees Celsius, and the calcination time was 2 hours to obtain a fired product. The sintered product was crushed by hand - after wet grinding with a ball mill, the particle size was -320 mesh. ) ammonium phosphate was decomposed for 3 hours, and the decomposition rate could reach 98.2%.
Embodiment 2
[0035] In a muffle furnace, add WO to 500 g 3 65% by weight of wolframite concentrate with a particle size of -320 mesh was added with 1.5 times the theoretical amount (ie, 210 g) of calcium carbonate, the reaction temperature was 1000 degrees Celsius, and the calcination time was 2 hours to obtain a fired product. The sintered product was crushed by hand - after wet grinding with a ball mill, the particle size was -320 mesh. ) ammonium phosphate is decomposed for 3 hours, and the decomposition rate can reach 99.5%.
Embodiment 3
[0037] In a muffle furnace, add WO to 500 g 3 65% by weight of wolframite concentrate with a particle size of -320 mesh was added with 1.4 times the theoretical amount (ie, 110 g) of calcium oxide, the reaction temperature was 1000 degrees Celsius, and the calcination time was 2 hours to obtain a fired product. The sintered product was crushed by hand - after wet grinding with a ball mill, the particle size was -320 mesh. ) ammonium phosphate was decomposed for 3 hours, and the decomposition rate could reach 99.1%.
PUM
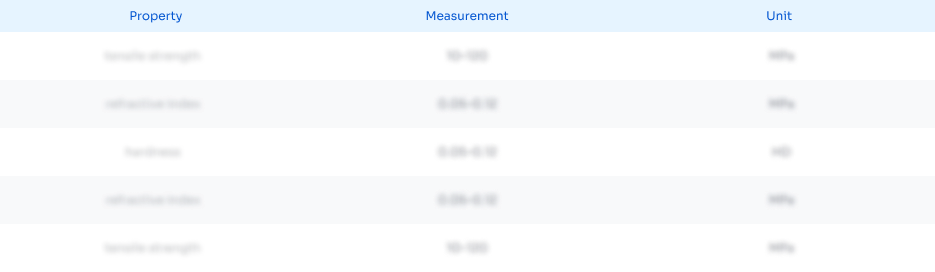
Abstract
Description
Claims
Application Information

- R&D
- Intellectual Property
- Life Sciences
- Materials
- Tech Scout
- Unparalleled Data Quality
- Higher Quality Content
- 60% Fewer Hallucinations
Browse by: Latest US Patents, China's latest patents, Technical Efficacy Thesaurus, Application Domain, Technology Topic, Popular Technical Reports.
© 2025 PatSnap. All rights reserved.Legal|Privacy policy|Modern Slavery Act Transparency Statement|Sitemap|About US| Contact US: help@patsnap.com