Energy-conservation high-efficiency reduction sponge iron tunnel kiln
A technology of sponge iron and tunnel kiln, which is applied to furnaces, furnace types, fluidized bed furnaces, etc., can solve the problems of changing one-way single-lane vehicle entry mode, difficult to control pressure and atmosphere, and large footprint, and achieve beneficial results. For preheating and cooling, compact structure, small footprint effect
- Summary
- Abstract
- Description
- Claims
- Application Information
AI Technical Summary
Problems solved by technology
Method used
Image
Examples
Embodiment Construction
[0010] As shown in the figure, take the company’s construction of a direct reduction iron tunnel kiln with an annual output of 50,000 tons as an example. I-shaped steel is used to make upright columns 8 on both sides of the kiln body and channel steel is used to make top beams 9 to form a frame. The brick structure is built between the columns 8 to form a kiln wall 11. The thickness of the kiln wall is 930 mm. Hanging pieces and hooks are used to build the ceiling bricks in the top beam 9 to form a kiln roof 10. The thickness of the kiln roof is 360 mm. The kiln is 86.53 meters long, the inner width of the kiln cavity is 5228 mm, and the inner height is 1972 mm. On the kiln wall 11, holes 14 for installing burners are set according to the distribution of burners in the combustion system. It is built with bricks 12, and the kiln foundation 18 at the bottom of the kiln cavity is provided with six rows of rails 15 for the kiln car 16 to run side by side with three lanes. Among th...
PUM
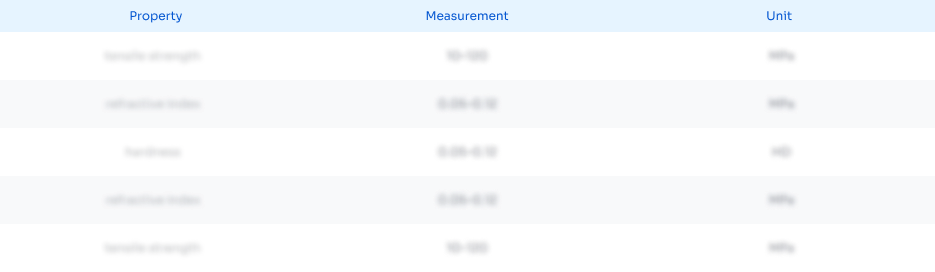
Abstract
Description
Claims
Application Information

- R&D
- Intellectual Property
- Life Sciences
- Materials
- Tech Scout
- Unparalleled Data Quality
- Higher Quality Content
- 60% Fewer Hallucinations
Browse by: Latest US Patents, China's latest patents, Technical Efficacy Thesaurus, Application Domain, Technology Topic, Popular Technical Reports.
© 2025 PatSnap. All rights reserved.Legal|Privacy policy|Modern Slavery Act Transparency Statement|Sitemap|About US| Contact US: help@patsnap.com