Process method for producing metal aluminium by high-alumina fly ash
A technology of high-alumina fly ash and process method, which is applied in the direction of process efficiency improvement, aluminum halide, aluminum chloride, etc., and can solve the problems of high corrosion resistance of equipment and materials, high production energy consumption, large lime dosage, etc. problems, to achieve the effect of solving the shortage of bauxite resources
- Summary
- Abstract
- Description
- Claims
- Application Information
AI Technical Summary
Problems solved by technology
Method used
Image
Examples
Embodiment Construction
[0030] Embodiments of the present invention: high aluminum fly ash of the present invention produces metal aluminum technological process such as figure 1 indicated,
[0031] The process is as follows: add high-alumina fly ash with 45% alumina content, add 30% concentration of hydrochloric acid, the ratio adopts the theoretical calculation value of alumina dissolution chemical reaction 1.0, the temperature of the raw coal slurry of fly ash is 25°C, and use the dissolution The feed pump is sent to the casing preheater of the dissolution device. The temperature of the material will reach 88°C after being preheated by the casing, and then heated to 150°C by the new steam casing preheater. The fresh steam temperature is 180°C and the pressure is 1.02MPa. . The raw ore slurry coming out of the new steam heating sleeve enters the autoclave for 45 minutes of heat preservation and dissolution. During the dissolution process of the autoclave, the dissolution rate of alumina in the fly...
PUM
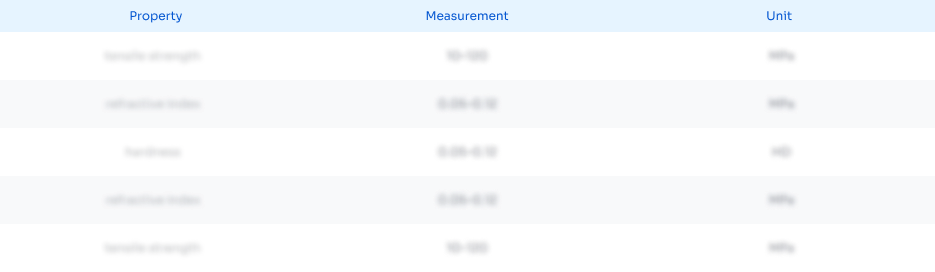
Abstract
Description
Claims
Application Information

- R&D Engineer
- R&D Manager
- IP Professional
- Industry Leading Data Capabilities
- Powerful AI technology
- Patent DNA Extraction
Browse by: Latest US Patents, China's latest patents, Technical Efficacy Thesaurus, Application Domain, Technology Topic, Popular Technical Reports.
© 2024 PatSnap. All rights reserved.Legal|Privacy policy|Modern Slavery Act Transparency Statement|Sitemap|About US| Contact US: help@patsnap.com