Process for dyeing and finishing cuprammonuium fabric
A copper ammonia fiber and process technology, which is applied in the field of fiber fabric processing technology, can solve the problems of easy swelling, fabric hardening and brittleness, and cross-section increase, and achieve the effect of complete treatment
- Summary
- Abstract
- Description
- Claims
- Application Information
AI Technical Summary
Problems solved by technology
Method used
Examples
Embodiment 1
[0045] The first step: pretreatment process
[0046] 1. Desizing process:
[0047] Put the cupro ammonia fiber in the normal temperature winding machine, start to heat up at room temperature, raise the temperature to 40°C, add desizing enzyme 2g / L and run for 10 minutes, add penetrant 1g / L, heat up to 80°C and run for 20 minutes to reach the bath The ratio is 1:20.
[0048] 2. Bleaching process
[0049] Drain the remaining desizing aid and water in the packaging machine. The first step: add soda ash to adjust the pH value to 11, and stir for 20 minutes until uniform; the second step: add 30% hydrogen peroxide 6g / L. Raise the temperature to 40°C, stir for 10 minutes, the third step: add stabilizer 2g / L, stir for 5 minutes, until uniform; the fourth step: add detergent 1g / L, stir for 10 minutes, liquor ratio 1:20;
[0050] 3. Enzyme washing and polishing process by air machine
[0051] Add 1 g / L of cellulase, run for 5 minutes; adjust the pH value to 4.5 with buffer acid, run...
Embodiment 2
[0068] The first step: pretreatment process
[0069] 1. Desizing process:
[0070] Put the cupro ammonia fiber in the normal temperature winding machine, start to heat up at room temperature, raise the temperature to 40°C, add desizing enzyme 3g / L and run for 10 minutes, add penetrant 2g / L, heat up to 80°C and run for 20 minutes to reach bath The ratio is 1:20.
[0071] 2. Bleaching process
[0072] Drain the remaining desizing aid and water in the packaging machine. The first step: add soda ash to adjust the pH value to 11, and stir for 20 minutes until uniform; the second step: add 30% hydrogen peroxide 6g / L. Raise the temperature to 40°C and stir for 10 minutes; Step 3: Add stabilizer 4g / L, stir for 5 minutes until uniform; Step 4: Add detergent 2g / L, stir for 10 minutes, liquor ratio 1:20;
[0073] 3. Enzyme washing and polishing process by air machine
[0074] Add 1 g / L of cellulase and run for 5 minutes; adjust the pH value to 5 with buffer acid, run for 5 minutes, ...
Embodiment 3
[0091] Pretreatment process
[0092] 1. Desizing process
[0093] Put the cupro ammonia fiber in the normal temperature winding machine, start to heat up at room temperature, raise the temperature to 40°C, add desizing enzyme 3g / L and run for 10 minutes, add penetrant 2g / L, heat up to 80°C and run for 20 minutes to reach bath The ratio is 1:20;
[0094] 2. Bleaching process
[0095] Drain the remaining desizing aid and water in the packaging machine. Step 1: Add soda ash to adjust the pH value to 10.5, and stir for 20 minutes until uniform; Step 2: Add 30% hydrogen peroxide 5g / L, and heat up to 40°C , and stir for 10 minutes; the third step: add stabilizer 3g / L, stir for 5 minutes until uniform; the fourth step: add detergent 2g / L, stir for 10 minutes, liquor ratio 1:20;
[0096] 3. Enzyme washing and polishing by airflow machine
[0097] Add 1 g / L cellulase, run for 5 minutes; adjust the pH value to 4.8 with buffer acid, run for 5 minutes, control the heating temperature ...
PUM
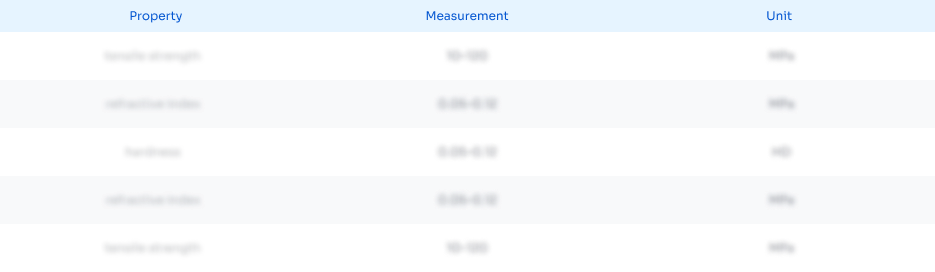
Abstract
Description
Claims
Application Information

- R&D Engineer
- R&D Manager
- IP Professional
- Industry Leading Data Capabilities
- Powerful AI technology
- Patent DNA Extraction
Browse by: Latest US Patents, China's latest patents, Technical Efficacy Thesaurus, Application Domain, Technology Topic, Popular Technical Reports.
© 2024 PatSnap. All rights reserved.Legal|Privacy policy|Modern Slavery Act Transparency Statement|Sitemap|About US| Contact US: help@patsnap.com