Method for increasing chlorate decomposition efficiency
A chlorate and efficiency technology, applied in the field of ion-exchange membrane caustic soda preparation, can solve the problems of unqualified caustic soda quality and unstable device operation, and achieve the effects of satisfying brine quality requirements and caustic soda quality requirements, improving decomposition efficiency, and heating uniformly
- Summary
- Abstract
- Description
- Claims
- Application Information
AI Technical Summary
Problems solved by technology
Method used
Image
Examples
Embodiment 1
[0027] The mass ratio of the light brine used to decompose chlorate to the light brine coming out of the electrolytic cell is 1:1.6, the peracidity of light brine after decomposing chlorate is 32g / l, and the chlorate content of imported light brine is 40g / l. The chlorate content at the outlet is 3.5g / l, the temperature of light brine in the decomposition tank is 97°C, and the decomposition rate is 93.75%.
[0028] Such as Figure 1~2 As shown, the steam heating tubes 1 in the chlorate decomposition tank are arranged in double layers, and the lower layer is used to spray gas upwards and the upper layer is to spray gas downwards. Steam nozzles 2 are evenly distributed on the steam heating tubes 1 .
[0029] process such as image 3 Shown:
[0030] The light brine from the light brine inlet 8 of the electrolytic cell is mixed with the 31% hydrochloric acid entering from the hydrochloric acid inlet 3 according to a certain ratio and then enters the chlorate decomposition tank 5....
Embodiment 2
[0032] The mass ratio of the light brine used to decompose chlorate to the light brine coming out of the electrolytic cell is 1:1.4, the peracidity of light brine after decomposing chlorate is 25g / l, and the chlorate content of imported light brine is 12g / l. The outlet chlorate content is 2g / l, the light brine temperature in the decomposition tank is 95°C, and the decomposition rate is 83%.
[0033] The structure and process flow of the steam heating pipe in the chlorate decomposition tank are as in Example 1.
Embodiment 3
[0035] The mass ratio of the light brine used to decompose chlorate to the light brine coming out of the electrolytic cell is 1:1.5, the peracidity of light brine after decomposing chlorate is 30g / l, and the chlorate content of imported light brine is 20g / l. The outlet chlorate content is 2g / l, the light brine temperature in the decomposition tank is 97°C, and the decomposition rate is 90%.
[0036] The structure and process flow of the steam heating pipe in the chlorate decomposition tank are as in Example 1.
PUM
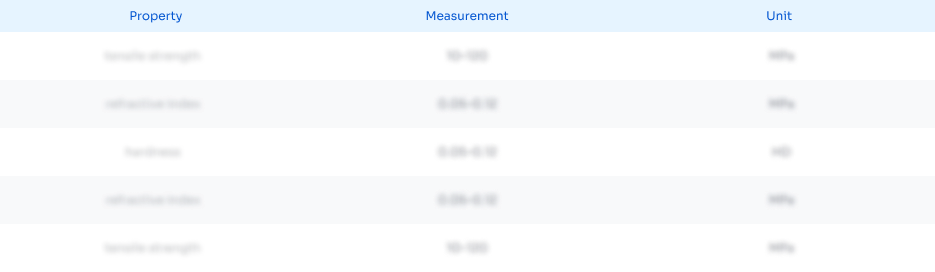
Abstract
Description
Claims
Application Information

- R&D
- Intellectual Property
- Life Sciences
- Materials
- Tech Scout
- Unparalleled Data Quality
- Higher Quality Content
- 60% Fewer Hallucinations
Browse by: Latest US Patents, China's latest patents, Technical Efficacy Thesaurus, Application Domain, Technology Topic, Popular Technical Reports.
© 2025 PatSnap. All rights reserved.Legal|Privacy policy|Modern Slavery Act Transparency Statement|Sitemap|About US| Contact US: help@patsnap.com