Series-parallel tilting drive mechanism of tilt rotor aircraft
A technology of tilting rotor and driving mechanism, which is applied in the field of hybrid tilting driving mechanism, can solve the problems of unfavorable rotor downwash airflow, poor lateral stability of aircraft, weakening propeller lift, etc. significant effect
- Summary
- Abstract
- Description
- Claims
- Application Information
AI Technical Summary
Problems solved by technology
Method used
Image
Examples
Embodiment Construction
[0018] Such as figure 1 , figure 2 As shown, the hybrid tilting drive mechanism is composed of a swing engine 1, a middle swing pulley 4, a swing transmission belt 5, a rotation engine 9, a wing rotation pulley 6, a rotation transmission belt 7, and a two-degree-of-freedom rotation mechanism 13. Two-degree-of-freedom rotating mechanism 13 is provided with frame 19, tie rod 18, center wheel 16, planetary gear 17, rotor swing belt pulley 15, rotor rotation belt pulley 12, and frame 19 is fixed on the wing 10 by support bar 11, The center wheel 16 and the tie rod 18 are installed on the frame 19, the tie rod 18 supports the planetary gear 17, the center wheel 16 and the planetary gear 17 mesh to form a gear pair, the rotor 14 is installed on the planetary wheel 17, the tie rod 18 and the rotor swing belt Wheel 15 is fixedly connected, and center wheel 16 is fixedly connected with rotor rotating belt pulley 12. The swing engine 1 and the middle swing pulley 4 are installed on t...
PUM
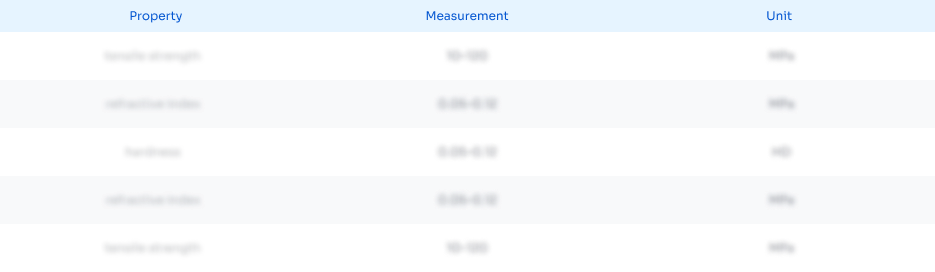
Abstract
Description
Claims
Application Information

- R&D Engineer
- R&D Manager
- IP Professional
- Industry Leading Data Capabilities
- Powerful AI technology
- Patent DNA Extraction
Browse by: Latest US Patents, China's latest patents, Technical Efficacy Thesaurus, Application Domain, Technology Topic, Popular Technical Reports.
© 2024 PatSnap. All rights reserved.Legal|Privacy policy|Modern Slavery Act Transparency Statement|Sitemap|About US| Contact US: help@patsnap.com