Turbine air-floatation main shaft
An air-floating spindle and air-floating bearing technology, applied in the field of energy and power, can solve the problems of limited application, poor natural heat dissipation conditions, thermal displacement of the shaft body and the shell, etc., and achieve high energy utilization rate, long working life, and stable rotation smooth effect
- Summary
- Abstract
- Description
- Claims
- Application Information
AI Technical Summary
Problems solved by technology
Method used
Image
Examples
Embodiment Construction
[0024] The principle, structure and working process of the present invention will be further described through the embodiments below in conjunction with the accompanying drawings.
[0025] refer to figure 1 , the turbine air-floating main shaft includes a shell that runs through the first end of the shell (ie figure 1 The shaft body 11 of the right end in), and the pneumatic turbine.
[0026] The casing is composed of an annular turbine base 8, a first end cover 2 connected to the first end of the turbine base 8, and a second end cover 16 connected to the second end of the turbine base 8. The second end cover 16 constitutes At the first end of the housing, an air cavity 3 is provided between the first end cover 2 and the first end of the turbine base 8, and the first end cover 2 is provided with an air inlet 1 communicating with the air cavity 3. Several exhaust holes 14 are arranged on the two end covers 16, and some exhaust holes 14 are preferably evenly distributed around...
PUM
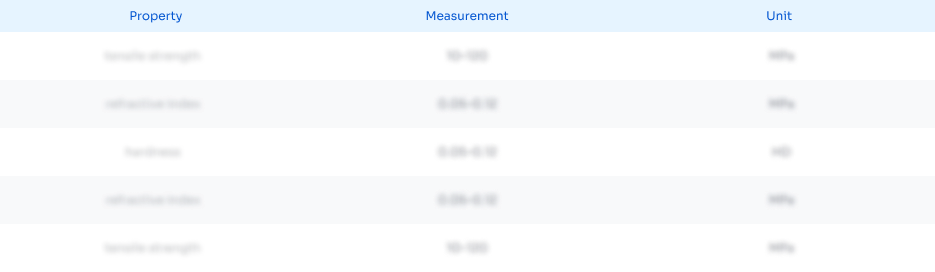
Abstract
Description
Claims
Application Information

- R&D
- Intellectual Property
- Life Sciences
- Materials
- Tech Scout
- Unparalleled Data Quality
- Higher Quality Content
- 60% Fewer Hallucinations
Browse by: Latest US Patents, China's latest patents, Technical Efficacy Thesaurus, Application Domain, Technology Topic, Popular Technical Reports.
© 2025 PatSnap. All rights reserved.Legal|Privacy policy|Modern Slavery Act Transparency Statement|Sitemap|About US| Contact US: help@patsnap.com