Polyvinyl chloride (PVC) decorative molded door panel and machining method thereof
A processing method and door panel technology, which is applied to wood processing appliances, door leaves, and other household appliances, can solve the problems of waste of wood resources, high production costs, and environmental pollution caused by fiber dust, so as to protect the ecological environment and achieve three-dimensional panels. Strong sense, the effect of reducing production costs
- Summary
- Abstract
- Description
- Claims
- Application Information
AI Technical Summary
Problems solved by technology
Method used
Image
Examples
Embodiment 1
[0024] A PVC facing molded door panel, including a panel and a PVC skin 1, the panel is a fiberboard 2 with concave-convex molding, and the fiberboard 2 formed by concave-convex molding forms grooves 3 The thickness of the fiberboard 2 is 2-4mm, and the fiberboard 2 is double-layered Composite structural fiberboard, PVC skin 1 is covered on the fiberboard 2.
[0025] The above-mentioned processing method of a PVC facing molded door panel comprises the following steps:
[0026] ①Use a steel mold to heat-press the wood fibers applied with glue and paraffin at a temperature of 150°C-180°C and a pressure of 800T for 2.5-3 minutes to form a fiber molded door panel, and the molded door after processing The thickness of the panel is 2-4mm;
[0027] ② Spray plastic glue on the surface of the molded door panel, the amount of glue sprayed is 65-90g / ㎡ and stored for 5-10 minutes;
[0028] ③Place the molded door panel after glue spraying on the template, the concave-convex shape under t...
Embodiment 2
[0031] A processing method for a PVC facing molded door panel comprises the following steps:
[0032] Choose 2-4mm flat MDF. The MDF is softened first. The softened MDF is placed in the mold of the hot press for hot pressing. After hot pressing, the fiber molded door panel is obtained. Other steps are the same as in Example 1.
PUM
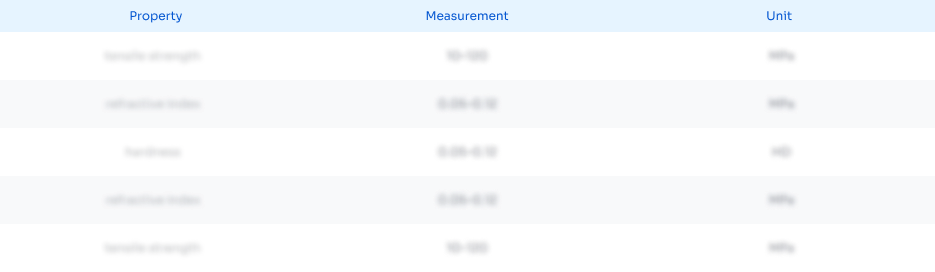
Abstract
Description
Claims
Application Information

- R&D
- Intellectual Property
- Life Sciences
- Materials
- Tech Scout
- Unparalleled Data Quality
- Higher Quality Content
- 60% Fewer Hallucinations
Browse by: Latest US Patents, China's latest patents, Technical Efficacy Thesaurus, Application Domain, Technology Topic, Popular Technical Reports.
© 2025 PatSnap. All rights reserved.Legal|Privacy policy|Modern Slavery Act Transparency Statement|Sitemap|About US| Contact US: help@patsnap.com