Coke quenching method for coke quenching furnace with gas-liquid two-phase distributor
A coke quenching furnace and phase distribution technology, which is applied in the field of coke quenching combined with dry quenching and wet quenching, can solve the problems of long coke cooling time, slow heat transfer between liquid and solid, poor coke quenching effect, etc. The effect of reducing temperature, uniform gas-liquid mixing, and maximizing sensible heat utilization
- Summary
- Abstract
- Description
- Claims
- Application Information
AI Technical Summary
Problems solved by technology
Method used
Image
Examples
specific Embodiment approach
[0026] According to the method of the present invention, the high-temperature mixed gas at about 850°C from the coke quenching oven is dedusted by the dust collector 31, and after the heat is recovered by the waste heat boiler 33, the temperature drops to 150°C, and the superheated steam produced by the waste heat boiler is exported from the superheated steam outlet 32 for external use; After the mixed gas at about 150°C passes through the waste heat boiler 33, it first passes through the heat pump 34, and the pressure increases. Part of the water vapor in the mixed gas releases heat and turns into liquid water, and the water vapor cools and releases heat to increase the temperature of the mixed gas; part of the gas enters the gas-liquid Separator 35; In the gas-liquid separator 35, the high-boiling point substances and water are condensed and separated from the gas, and the separated gas is sent to the gas-liquid two-phase distributor 22 in the coke quenching oven through the...
Embodiment 1
[0029] The coke quenching method of the present invention uses the gas-liquid two-phase distributor 22 inside the coke quenching oven to realize simultaneous gas-liquid distribution and coke quenching. After the gas passes through the gas-liquid two-phase distributor 22, the gas is distributed by the gas-liquid two-phase distributor 22 1 The gas outlet 17 of the annular support ring 7 flows out evenly, and the conical carbon baffle plate 8 is evenly distributed in the cooling medium distribution area 29, and rises into the first cooling area 21 to evenly distribute the coke quenching, so that the first cooling area of the coke quenching oven 21. The temperature of the coke decreases continuously during the descent process. When the coke enters the cooling medium distribution area 29, the temperature is about 400°C; the coke accumulated on the circular baffle plate 6 of the gas-liquid two-phase distributor, When the gas distribution tower 1 of the phase distributor 22 rotates,...
Embodiment 2
[0031] The conditions of the experimental device of the embodiment of the present invention are: the height of the high-temperature coke pre-storage area 19 is 900 mm, the inner diameter is 600 mm, the cover is a steel plate lined with heat-insulating material, there is a valve at the connection between the high-temperature coke pre-storage area 19 and the cooling area, and the inner diameter of the valve is Ф300, There are 150mm high and 45°C inclined conical cylinders at the top and bottom, so that the gas can be better exported to the quenching oven; when coke is put into the high-temperature coke pre-storage area 19, the valve is closed and opened at 5mm below the valve. There is a high-temperature mixed gas outlet 30; the height of the cooling zone is 1200mm, the inner diameter is 600mm, the height of the discharge zone 24 is 300mm, and the outlet diameter is 150mm; the bottom of the gas-liquid two-phase distributor 22 with three conical carbon baffles 8 is located at a dis...
PUM
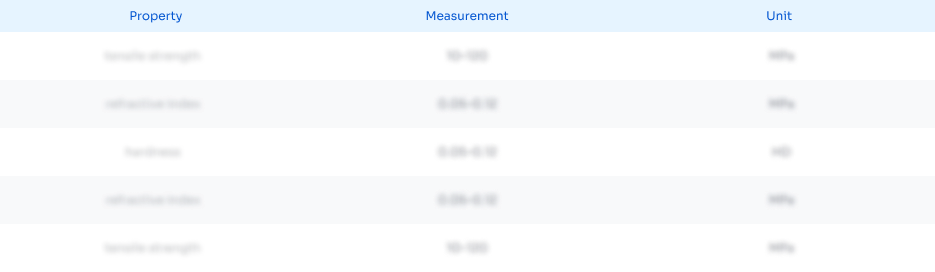
Abstract
Description
Claims
Application Information

- Generate Ideas
- Intellectual Property
- Life Sciences
- Materials
- Tech Scout
- Unparalleled Data Quality
- Higher Quality Content
- 60% Fewer Hallucinations
Browse by: Latest US Patents, China's latest patents, Technical Efficacy Thesaurus, Application Domain, Technology Topic, Popular Technical Reports.
© 2025 PatSnap. All rights reserved.Legal|Privacy policy|Modern Slavery Act Transparency Statement|Sitemap|About US| Contact US: help@patsnap.com