Method for producing thermoplastic composite material and double steel-belt continuous press
A technology of composite materials and double steel strips, applied in the direction of chemical instruments and methods, lamination, layered products, etc., to achieve the effects of increasing strength, saving investment costs, and reducing manufacturing costs
- Summary
- Abstract
- Description
- Claims
- Application Information
AI Technical Summary
Problems solved by technology
Method used
Image
Examples
Embodiment Construction
[0018] according to figure 1 As shown, the present invention includes a set of paper loading system D, and a set of preheating and pressurizing system C and the main press are added on the driven roller at the entrance of the main press; the main press mainly includes a vertically symmetrical A group of driven rollers 12, a group of driving rollers 19 and a steel belt 18 wrapped around them are divided into a heating section A and a cooling section B; the driven rollers 12 and driving rollers 19 are respectively located at both ends of the press , is connected with the frame 17, the heating section A and the cooling section B are located inside the frame 17, and are connected with the frame 17 to form two sets of heating and cooling systems that are symmetrical up and down; Steel belt 18 on driven roller 12.
[0019] Among them, the paper loading system D such as figure 2 As shown, there are two sets of laminated paper rolls 4, two sets of first surface layer paper rolls, ...
PUM
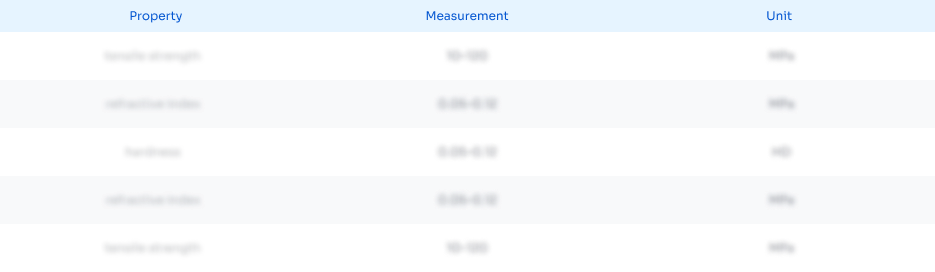
Abstract
Description
Claims
Application Information

- R&D Engineer
- R&D Manager
- IP Professional
- Industry Leading Data Capabilities
- Powerful AI technology
- Patent DNA Extraction
Browse by: Latest US Patents, China's latest patents, Technical Efficacy Thesaurus, Application Domain, Technology Topic, Popular Technical Reports.
© 2024 PatSnap. All rights reserved.Legal|Privacy policy|Modern Slavery Act Transparency Statement|Sitemap|About US| Contact US: help@patsnap.com