Light source module and area light source module using the same
A light source module, surface light source technology, applied in the direction of light source, electric light source, point light source, etc., can solve the problem of affecting the service life of the light-emitting element, the luminous efficiency of the light-emitting element, etc.
- Summary
- Abstract
- Description
- Claims
- Application Information
AI Technical Summary
Problems solved by technology
Method used
Image
Examples
Embodiment Construction
[0044] In the light source module and the surface light source module of this embodiment, one end of the heat pipe is connected to the heat sink to absorb heat from the heat sink, and the other end of the heat pipe extends outward from the heat sink to release heat. The cooling liquid in the heat pipe can evaporate upward after being heated at the heat-absorbing end and move toward the heat-dissipating end. After the steam condenses and releases heat, it becomes a liquid and flows downward through the siphon to the heat-absorbing end. Such a continuous periodic cycle can quickly dissipate the heat absorbed by the heat sink through the cooling liquid to achieve the cooling effect.
[0045] Please refer to figure 1 , Figure 2A , Figure 2B and Figure 2C ,in figure 1 A schematic diagram illustrating a light source module according to an embodiment, Figure 2A , Figure 2B and Figure 2C The cross-sectional schematic diagrams of different types of grooves are respectively...
PUM
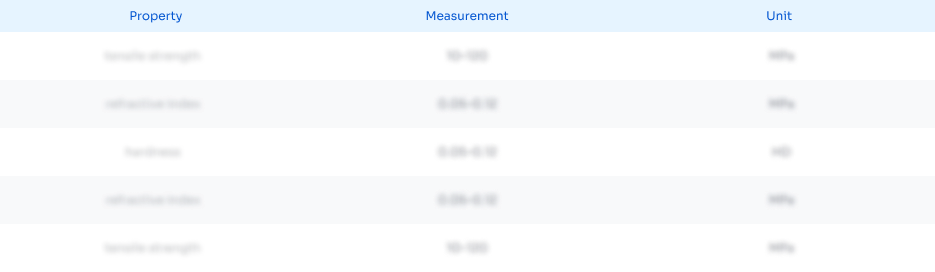
Abstract
Description
Claims
Application Information

- R&D
- Intellectual Property
- Life Sciences
- Materials
- Tech Scout
- Unparalleled Data Quality
- Higher Quality Content
- 60% Fewer Hallucinations
Browse by: Latest US Patents, China's latest patents, Technical Efficacy Thesaurus, Application Domain, Technology Topic, Popular Technical Reports.
© 2025 PatSnap. All rights reserved.Legal|Privacy policy|Modern Slavery Act Transparency Statement|Sitemap|About US| Contact US: help@patsnap.com