Gear steel and heat treatment method thereof
A heat treatment method and gear technology, applied in the field of metallurgy, can solve the problems of low austenite grain size and large dispersion
- Summary
- Abstract
- Description
- Claims
- Application Information
AI Technical Summary
Problems solved by technology
Method used
Image
Examples
Embodiment 1-14
[0035] The components of the gear steels of Examples 1-14 are shown in Table 5. The heat treatment method is as follows: after normalizing the blank at 925±5°C for 40-60 minutes, make a Φ25±0.5mm standard sample, and end quenching temperature at 925°C±5°C for 30±5 minutes at the end .
[0036] Table 5 Embodiment 1-14 Composition of gear steel
[0037]
[0038] According to JIS G0551, the austenite grain size of the gear steels of Examples 1-14 is as shown in Table 6, and the grain size grades of the gear steels of Examples 1-14 are all greater than 6 grades. According to GB / T225, the hardenability test is carried out on the steels of different specifications of the gear steels of Examples 1-14, and the experimental results are as shown in Table 6. It can be seen that the hardenability of the steel for gears of the present invention is J3, J8, J13, J30, J405 Point bandwidth (the calculation method adopts GB / T225-2006 / ISO642:1999) is controlled below 5RCH. From Examples 1-...
Embodiment 15
[0043] Using the steel for gears of Examples 1-14 to produce gears by forging, the produced gears are applied to automobiles or motorcycles, which can reduce the deformation of broken teeth and improve the service life of gears
PUM
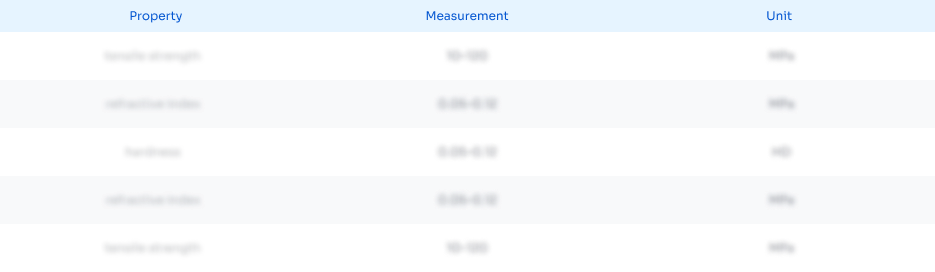
Abstract
Description
Claims
Application Information

- R&D Engineer
- R&D Manager
- IP Professional
- Industry Leading Data Capabilities
- Powerful AI technology
- Patent DNA Extraction
Browse by: Latest US Patents, China's latest patents, Technical Efficacy Thesaurus, Application Domain, Technology Topic, Popular Technical Reports.
© 2024 PatSnap. All rights reserved.Legal|Privacy policy|Modern Slavery Act Transparency Statement|Sitemap|About US| Contact US: help@patsnap.com