Guide track unloading device for crossbeam of large-sized machine tool and deflection compensation method
An unloading device, beam technology, applied in metal processing machinery parts, other manufacturing equipment/tools, maintenance and safety accessories, etc., can solve the problems of beam reference guide rail deformation, deflection deformation, inability to effectively compensate beam deflection deformation, etc. , to achieve stable and reliable operation
- Summary
- Abstract
- Description
- Claims
- Application Information
AI Technical Summary
Problems solved by technology
Method used
Image
Examples
Embodiment Construction
[0027] Below in conjunction with accompanying drawing, the present invention is further described:
[0028] A method for deflection compensation and guide rail unloading compensation for beams of large machine tools, characterized in that the specific steps are as follows:
[0029] 1) Determination of compensation distance and compensation point: According to the deflection and deformation of the cantilever (simply supported) beam, through theoretical calculation, according to the principle of slope approximation, the unloading beam 2 is divided into several compensation distances, and the distance between adjacent compensation points According to the straight line processing, and the cross-section of the upper surface of the unloading beam 2 is composed of several straight lines, the upper surface of the unloading beam 2 is processed according to the value determined by the calculation result;
[0030] 2) Determination of the electrical compensation value: collect the straigh...
PUM
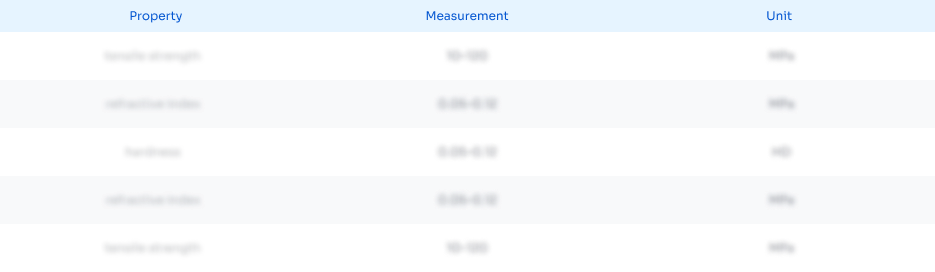
Abstract
Description
Claims
Application Information

- R&D
- Intellectual Property
- Life Sciences
- Materials
- Tech Scout
- Unparalleled Data Quality
- Higher Quality Content
- 60% Fewer Hallucinations
Browse by: Latest US Patents, China's latest patents, Technical Efficacy Thesaurus, Application Domain, Technology Topic, Popular Technical Reports.
© 2025 PatSnap. All rights reserved.Legal|Privacy policy|Modern Slavery Act Transparency Statement|Sitemap|About US| Contact US: help@patsnap.com