Blank of automotive front pillar inner plate part and machining method
A column and blank technology is applied in the field of steel plate blanks and processing of the inner plate of the front column of an automobile, and can solve the problems of many wastes, high cost, and many processes.
- Summary
- Abstract
- Description
- Claims
- Application Information
AI Technical Summary
Problems solved by technology
Method used
Image
Examples
Embodiment Construction
[0017] The present invention will be further described below in conjunction with the accompanying drawings.
[0018] Such as image 3 As shown, the shape structure of the front pillar inner panel blank is based on the shape characteristics of the front pillar inner panel parts. In order to improve the material utilization rate, it is designed as a polygonal shape blank 3 whose edge is closer to the part. The polygonal shape blank 3 The middle section is straight, one end is wide, and the other end is narrow; the left and right ends are bent toward the same side, and the curved part 4 adopts a circular arc transition to avoid stress concentration at the sharp corner during subsequent processing.
[0019] Such as Figure 4 As shown, compared with the rectangular structure blank, the polygonal shape blank 3 is closer to the effective surface of the inner panel part 1 of the front pillar, which improves the material utilization rate of the part and reduces the generation of waste...
PUM
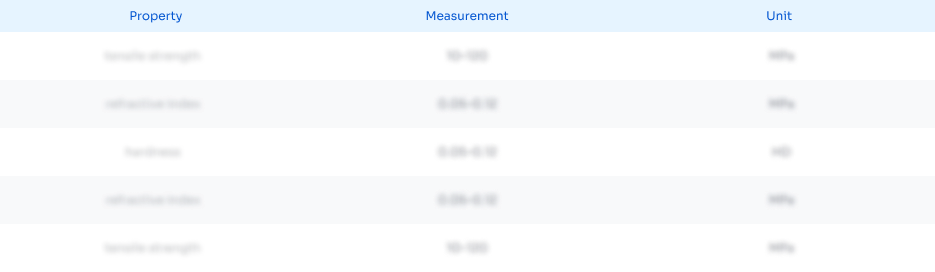
Abstract
Description
Claims
Application Information

- Generate Ideas
- Intellectual Property
- Life Sciences
- Materials
- Tech Scout
- Unparalleled Data Quality
- Higher Quality Content
- 60% Fewer Hallucinations
Browse by: Latest US Patents, China's latest patents, Technical Efficacy Thesaurus, Application Domain, Technology Topic, Popular Technical Reports.
© 2025 PatSnap. All rights reserved.Legal|Privacy policy|Modern Slavery Act Transparency Statement|Sitemap|About US| Contact US: help@patsnap.com