Preparation method of electrolyte used in all-vanadium redox flow battery
A technology for the preparation of all-vanadium redox flow batteries and electrolytes, applied in the direction of regenerative fuel cells, etc., can solve the problems of vanadium resources not being well utilized, reduce harmful gas emissions, reduce production costs, and reduce environmental pollution Effect
- Summary
- Abstract
- Description
- Claims
- Application Information
AI Technical Summary
Problems solved by technology
Method used
Image
Examples
Embodiment 1
[0048] 100gV 2 O 5 The powder and 300g of sodium carbonate were roasted in an oxygen-enriched rotary kiln at 800°C for 2 hours. They were leached three times with 300mL of water at a temperature of 80°C, and then filtered. The leaching time was 20 minutes each time; the three filtrates were combined to obtain a bias. 900mL of sodium vanadate leaching solution; adding a small amount of sodium carbonate solid to the leaching solution to adjust the pH to 10, stirring and filtering to obtain 1000mL filtrate; adding a small amount of calcium chloride to the resulting filtrate, stirring and filtering to obtain 1100mL filtrate; adding a small amount of aluminum sulfate to the resulting filtrate After stirring, filter to obtain 1200mL filtrate; add 0.5N sulfuric acid to adjust the pH value of the obtained filtrate to 3, and add 80mL concentrated hydrochloric acid to the resulting sodium metavanadate solution to undergo redox reaction to obtain 1200mL0.41mol / L vanadyl sulfate VOSO 4 Solut...
Embodiment 2
[0050] 100gV 2 O 5 The powder and 300g of sodium carbonate were roasted in an oxygen-enriched rotary kiln at 800°C for 2 hours. They were leached three times with 300mL of water at a temperature of 85°C and then filtered. The leaching time was 20 minutes each time; the three filtrates were combined to obtain a partial 900mL of sodium vanadate leaching solution; adding a small amount of sodium carbonate solid to the leaching solution to adjust the pH to 10, stirring and filtering to obtain 1000mL filtrate; adding a small amount of calcium chloride to the resulting filtrate, and filtering after stirring to obtain 1100mL filtrate; adding a small amount of aluminum sulfate to the resulting filtrate After stirring, filter to obtain 1200mL filtrate; add 0.5N sulfuric acid to adjust the pH of the obtained filtrate to 3, and add 80mL concentrated hydrochloric acid to the resulting sodium metavanadate solution to undergo redox reaction to obtain 1200mL0.43mol / L vanadyl sulfate VOSO 4 Solu...
Embodiment 3
[0052] 10kgV 2 O 5 The converter vanadium slag solid is mixed with 2.0kg sodium carbonate and roasted in an oxygen-rich rotary kiln at 780℃ for 3 hours; after roasting, the reaction mixture is leached three times with 100L of water at 90℃ to extract sodium vanadate in the solid reaction mixture. The extraction time is 30 minutes. After each extraction, it is loaded in a hopper with a filter cloth and a solution collector at the bottom. The three filtrates are combined to obtain 100L of sodium metavanadate extract; a small amount of sodium carbonate solid is added to the extract to adjust the pH value 13.5. After stirring in the reactor for a period of time, it is also poured into a hopper with a filter cloth and a solution collector at the bottom, and filtered to obtain 100L of filtrate; the filtrate is added with a small amount of calcium chloride and stirred in the reactor for a period of time, and then poured into the bottom for filtration. In the hopper of the cloth and solu...
PUM
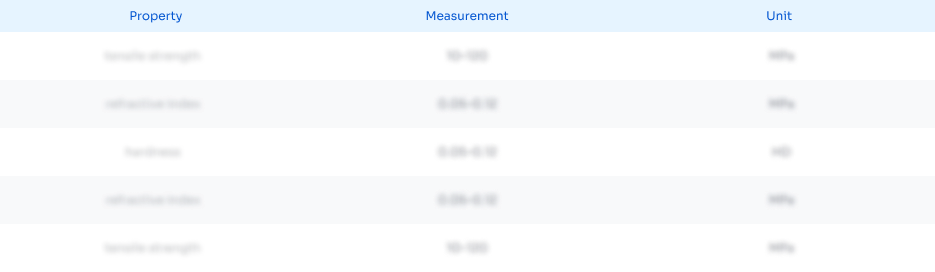
Abstract
Description
Claims
Application Information

- R&D
- Intellectual Property
- Life Sciences
- Materials
- Tech Scout
- Unparalleled Data Quality
- Higher Quality Content
- 60% Fewer Hallucinations
Browse by: Latest US Patents, China's latest patents, Technical Efficacy Thesaurus, Application Domain, Technology Topic, Popular Technical Reports.
© 2025 PatSnap. All rights reserved.Legal|Privacy policy|Modern Slavery Act Transparency Statement|Sitemap|About US| Contact US: help@patsnap.com