Optical fiber loop framework and winding method thereof
An optical fiber loop and skeleton technology, applied in Sagnac effect gyroscopes and other directions, can solve the problem that the advantages of quadrupole symmetry and improved winding method cannot be fully utilized, the influence of reciprocity winding process consistency, and the inability to guarantee each Layer turns consistency and other issues, to achieve the effect of efficient batch winding, automated process promotion, and reduced human intervention
- Summary
- Abstract
- Description
- Claims
- Application Information
AI Technical Summary
Problems solved by technology
Method used
Image
Examples
Embodiment Construction
[0026] Below in conjunction with accompanying drawing, specific embodiment of the present invention is described in further detail:
[0027] Such as figure 1 and figure 2 As shown, an optical fiber ring frame of the present invention includes a frame body 1 with an annular groove on the rim, and the groove bottom 2 of the frame body 1 is provided with several fiber grooves along the winding direction of the optical fiber. The distance is consistent with the diameter of the optical fiber to be wound; the side wall 3 of the skeleton body 1 is provided with several convex and concave positioning protrusions and positioning grooves along the winding direction of the optical fiber. And on the two side walls 3, the convex and concave are opposite at the same distance from the bottom 2 of the groove. In order to facilitate the subsequent use of the optical fiber ring, a flange 4 is provided on the inner surface of the skeleton body 1, which can be used for fixing with other compo...
PUM
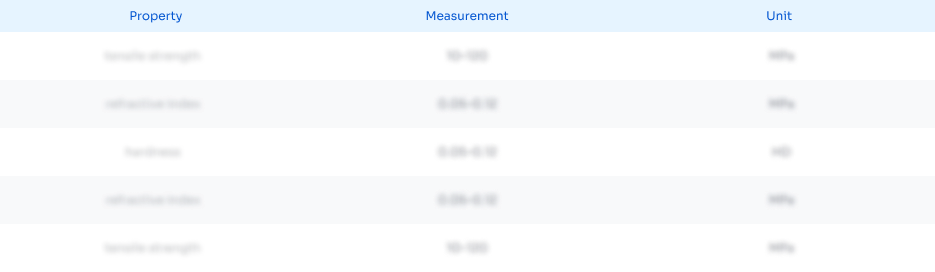
Abstract
Description
Claims
Application Information

- Generate Ideas
- Intellectual Property
- Life Sciences
- Materials
- Tech Scout
- Unparalleled Data Quality
- Higher Quality Content
- 60% Fewer Hallucinations
Browse by: Latest US Patents, China's latest patents, Technical Efficacy Thesaurus, Application Domain, Technology Topic, Popular Technical Reports.
© 2025 PatSnap. All rights reserved.Legal|Privacy policy|Modern Slavery Act Transparency Statement|Sitemap|About US| Contact US: help@patsnap.com