Metal powder flux-cored wire for high-strength steel
A technology of flux-cored welding wire and high-strength steel, applied in metal processing equipment, welding media, welding equipment, etc., can solve the problems of not allowing cellulose-type electrodes, high strength, and high sensitivity to cold cracks, and achieve high welding melting Deposition efficiency and deposition speed, improvement of thermal cracking resistance, reduction of welding fume and spatter
- Summary
- Abstract
- Description
- Claims
- Application Information
AI Technical Summary
Problems solved by technology
Method used
Image
Examples
Embodiment Construction
[0018] A metal powder-type flux-cored wire for high-strength steel, which uses low-P, S low-carbon steel strips as the wire sheath, uses a flux-cored transition alloy, and is manufactured using a general-purpose flux-cored wire manufacturing process. The filling ratio is 10%-20%.
[0019] Select the cold-rolled steel strip, and use the total mass composition of the matching welding wire as shown in Table 1:
[0020] Table 1: Embodiment ①~⑥ drug core composition
[0021]
[0022] The diameter of the welding wire is 1.2mm. After the above-mentioned flux-cored welding wire is made, it is connected with DC reverse, the voltage is 28V, the current is 250A, the dry elongation is 18mm, and the moving speed is 250mm / min. The mechanical properties of the weld are shown in Table 2.
[0023] Table 2 Examples ① ~ ⑥ obtained weld mechanical properties
[0024]
PUM
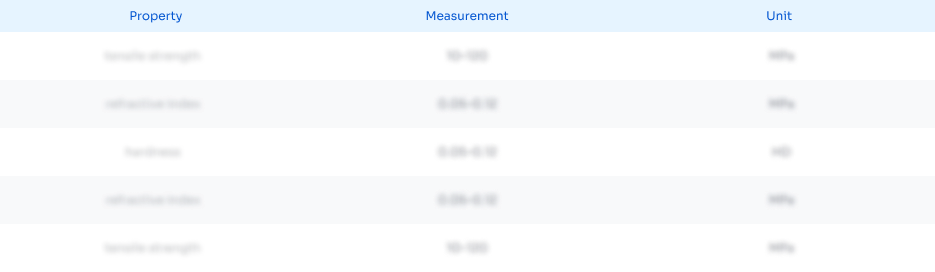
Abstract
Description
Claims
Application Information

- R&D
- Intellectual Property
- Life Sciences
- Materials
- Tech Scout
- Unparalleled Data Quality
- Higher Quality Content
- 60% Fewer Hallucinations
Browse by: Latest US Patents, China's latest patents, Technical Efficacy Thesaurus, Application Domain, Technology Topic, Popular Technical Reports.
© 2025 PatSnap. All rights reserved.Legal|Privacy policy|Modern Slavery Act Transparency Statement|Sitemap|About US| Contact US: help@patsnap.com