Large steel ladle and manufacturing method for same
A manufacturing method and ladle technology, applied in the direction of manufacturing tools, casting equipment, casting melt containers, etc., can solve the problems of affecting the operation cycle of ladles, long repair or replacement time, and large consumption of refractory materials, so as to save manpower and material resources, High construction efficiency and less material consumption
- Summary
- Abstract
- Description
- Claims
- Application Information
AI Technical Summary
Problems solved by technology
Method used
Image
Examples
Embodiment 1
[0017] like figure 2 As shown in the figure, the large ladle of this embodiment includes a clad body with an open top, and the bottom of the clad body is provided with a ventilation brick 2 and a molten steel nozzle 3. The castable is casted to form the permanent layer 1 and the inner lining, the bottom half of the inner lining and the lower half of the side are made of corundum spinel castable 7, and the upper half of the side of the inner lining is magnesium The carbon bricks 4 are built by masonry, and the top of the inner lining layer is provided with a seal 6 .
[0018] The large ladle of the present embodiment, when specifically manufactured, includes the following steps:
[0019] The first step is to pour the permanent layer: first place the breathable brick model and the nozzle model at the bottom of the ladle, pour the bottom permanent layer with a mixture of aluminum-magnesium castable and water, and cure under natural conditions. After the castable reaches the dem...
Embodiment 2
[0031] In the large ladle of this embodiment, the upper half of the side surface of the inner lining layer is built by mixing magnesia-carbon bricks 4 and carbon-free prefabricated blocks. Other structures and manufacturing methods are the same as those in Embodiment 1.
PUM
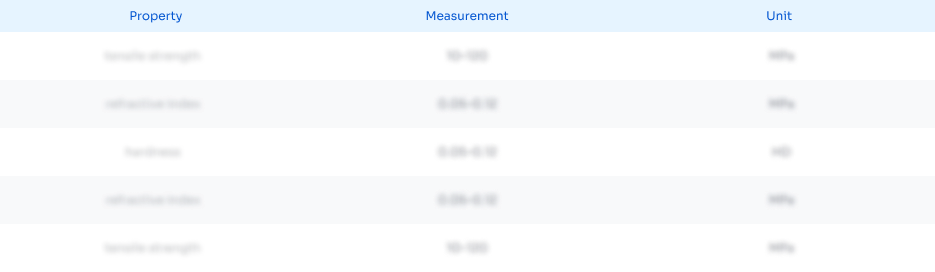
Abstract
Description
Claims
Application Information

- R&D Engineer
- R&D Manager
- IP Professional
- Industry Leading Data Capabilities
- Powerful AI technology
- Patent DNA Extraction
Browse by: Latest US Patents, China's latest patents, Technical Efficacy Thesaurus, Application Domain, Technology Topic, Popular Technical Reports.
© 2024 PatSnap. All rights reserved.Legal|Privacy policy|Modern Slavery Act Transparency Statement|Sitemap|About US| Contact US: help@patsnap.com