Cascading gain self-scheduling PID (Proportion Integration Differentiation) controller
A self-scheduling and controller technology, applied in the direction of electric controllers, controllers with specific characteristics, etc., to achieve the effects of reducing dynamic deviation and static deviation, good robustness, and shortening transition time
- Summary
- Abstract
- Description
- Claims
- Application Information
AI Technical Summary
Problems solved by technology
Method used
Image
Examples
Embodiment Construction
[0023] see figure 1 , figure 1 It is a simplified structural diagram of the cascade gain self-scheduling PID controller of the present invention.
[0024] The cascade gain self-scheduling PID controller includes: a PID gain self-scheduling inner control loop 10, a detection and tuning loop 20 and a PID gain self-scheduling outer control loop 30, and the detection and tuning loop 20 is respectively connected to the PID gain self-scheduling Inner control loop 10 and said PID gain self-scheduling outer control loop 30;
[0025] The PID gain self-scheduling inner control loop 10 includes an inner loop PID gain self-scheduling controller and an inner loop control mode switch 15, and the input end of the inner loop control mode switch 15 is connected to the inner loop PID gain self-scheduling control The output terminal of the device, its control terminal is connected to the output terminal of the detection and setting loop 20;
[0026] The PID gain self-scheduling outer control ...
PUM
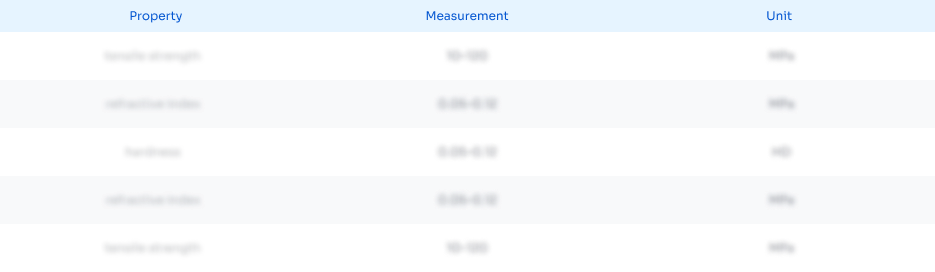
Abstract
Description
Claims
Application Information

- R&D Engineer
- R&D Manager
- IP Professional
- Industry Leading Data Capabilities
- Powerful AI technology
- Patent DNA Extraction
Browse by: Latest US Patents, China's latest patents, Technical Efficacy Thesaurus, Application Domain, Technology Topic, Popular Technical Reports.
© 2024 PatSnap. All rights reserved.Legal|Privacy policy|Modern Slavery Act Transparency Statement|Sitemap|About US| Contact US: help@patsnap.com