Full-automatic multi-station welding system
A welding system and multi-station technology, applied in the direction of welding equipment, auxiliary welding equipment, welding/cutting auxiliary equipment, etc., can solve the problem of no automatic coating and feeding mechanism, short life, automatic identification and automatic sorting cannot be realized And other issues
- Summary
- Abstract
- Description
- Claims
- Application Information
AI Technical Summary
Problems solved by technology
Method used
Image
Examples
Embodiment Construction
[0041] The present invention is a full-automatic multi-station welding system. The main technical solution is: the turntable and the transmission device 51 (including the switch), and sensors are installed at both ends of the flat vibration to detect the workpiece and the vibrating plate stops working when the material is full. The way to continue working, manipulator assembly, contact bridge storage and feeding device, contact feeding and feeding device (including front and back recognition and sorting devices when contact feeding, solder dripping device, contact cross-propelling device), The output part.
[0042] refer to figure 1 , figure 2 , image 3 , a turntable and a transmission device 51 are installed on the base 53, the turntable and the transmission device 51 are set according to the inner and outer indexing of the four-station circular ring divided into eight equal parts, including the outer turntable 5103 and the inner disc 5102, and the inner disc 5102 axis A...
PUM
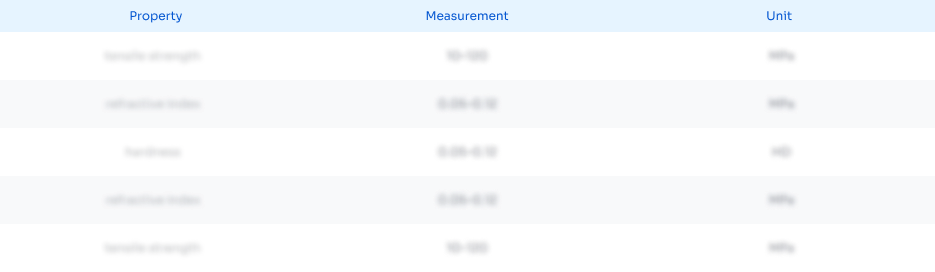
Abstract
Description
Claims
Application Information

- R&D
- Intellectual Property
- Life Sciences
- Materials
- Tech Scout
- Unparalleled Data Quality
- Higher Quality Content
- 60% Fewer Hallucinations
Browse by: Latest US Patents, China's latest patents, Technical Efficacy Thesaurus, Application Domain, Technology Topic, Popular Technical Reports.
© 2025 PatSnap. All rights reserved.Legal|Privacy policy|Modern Slavery Act Transparency Statement|Sitemap|About US| Contact US: help@patsnap.com