Temperature drift compensation optical current transformer and current compensation method thereof
A current transformer and temperature drift technology, applied in the field of transformers, can solve the problems of optical current transformer measurement accuracy temperature drift, etc.
- Summary
- Abstract
- Description
- Claims
- Application Information
AI Technical Summary
Problems solved by technology
Method used
Image
Examples
specific Embodiment approach 1
[0043]DETAILED DESCRIPTION OF THE PREFERRED EMBODIMENTS 1. A temperature drift compensation optical current transformer, which includes a housing 1, an optical sensor 2, a first multimode optical fiber 3, a polarization maintaining optical fiber 4, a base 6, a signal processing unit 7 and a second multimode optical fiber 8. The optical sensor 2 is fixed inside the casing 1, which is characterized in that it also includes a solenoid-type self-induction sensor 5,
[0044] One end of the optical sensor 2 is connected to one end of the solenoid-type self-inductance sensor 5 through a polarization-maintaining optical fiber 4, and the other end of the solenoid-type self-inductance sensor 5 is connected to the signal processing unit 7 through a second multimode optical fiber 8, and the optical sensor The other end of 2 is connected to the signal processing unit 7 through the first multimode optical fiber 3, the solenoid type self-inductance sensor 5 and the signal processing unit 7 ar...
specific Embodiment approach 2
[0048] Specific embodiment two, temperature drift current compensation method, it comprises the following steps:
[0049] Step 1. The Faraday rotation angle generated by the linearly polarized light of the optical sensor 2 according to the Faraday magneto-optical effect With the current to be measured i 1 Expressed as:
[0050]
[0051] In the formula: is the Faraday rotation angle generated by the linearly polarized light passing through the optical sensor 2; is a constant proportional coefficient; V 1 Be the Verdet constant of the first magneto-optical glass 2-3 under normal temperature; i 1 is the current to be measured,
[0052] Step 2, the Faraday rotation angle produced by the linearly polarized light of the solenoid type self-inductance sensor 5 according to the Faraday magneto-optic effect With the current to be measured i 2 Expressed as:
[0053]
[0054] In the formula: is the Faraday rotation angle generated by the linearly polarized light throug...
PUM
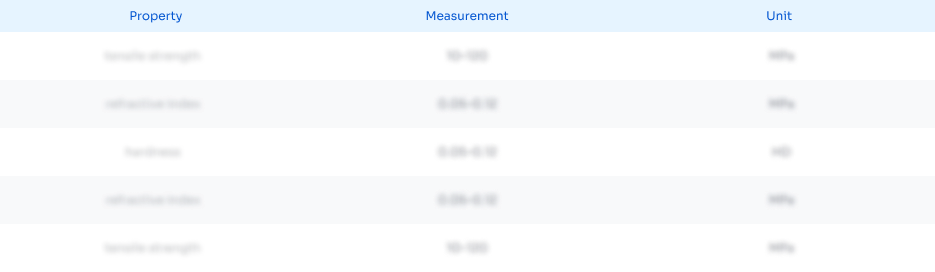
Abstract
Description
Claims
Application Information

- R&D
- Intellectual Property
- Life Sciences
- Materials
- Tech Scout
- Unparalleled Data Quality
- Higher Quality Content
- 60% Fewer Hallucinations
Browse by: Latest US Patents, China's latest patents, Technical Efficacy Thesaurus, Application Domain, Technology Topic, Popular Technical Reports.
© 2025 PatSnap. All rights reserved.Legal|Privacy policy|Modern Slavery Act Transparency Statement|Sitemap|About US| Contact US: help@patsnap.com