Distributed type electronic hydraulic brake system using isolating valves
A hydraulic brake and isolation valve technology, applied in the direction of brakes, brake transmissions, transportation and packaging, etc., can solve the problem of braking deviation and braking stability, causing risks, and failure to meet braking stability and braking performance and other issues to achieve the effect of ensuring braking efficiency and braking stability and improving system reliability
- Summary
- Abstract
- Description
- Claims
- Application Information
AI Technical Summary
Problems solved by technology
Method used
Image
Examples
Embodiment Construction
[0011] A distributed electro-hydraulic braking system using an isolation valve proposed by the present invention has a structure such as figure 2 As shown, including right front brake actuator 1, left front brake actuator 2, right rear brake actuator 3, left rear brake actuator 4, right front brake 5, left front brake 6, right rear brake 7, left rear brake 8. Right front brake actuator controller 9, left front brake actuator controller 10, right rear brake actuator controller 11, left rear brake actuator controller 12, brake pedal 15, pedal sensor 16, wire Control the brake controller 17 and the bus 18, which is characterized in that the hydraulic cylinders of the right front brake actuator 1, the left front brake actuator 2, the right rear brake actuator 3 and the left rear brake actuator 4 are respectively provided with There are a first oil outlet and a second oil outlet, and the distributed electronic hydraulic braking system also includes a front axle brake actuator isol...
PUM
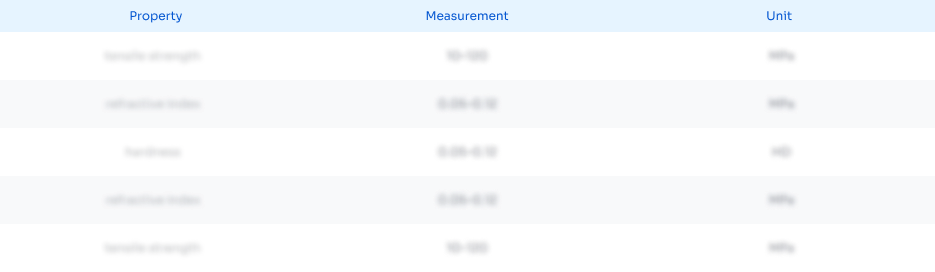
Abstract
Description
Claims
Application Information

- R&D
- Intellectual Property
- Life Sciences
- Materials
- Tech Scout
- Unparalleled Data Quality
- Higher Quality Content
- 60% Fewer Hallucinations
Browse by: Latest US Patents, China's latest patents, Technical Efficacy Thesaurus, Application Domain, Technology Topic, Popular Technical Reports.
© 2025 PatSnap. All rights reserved.Legal|Privacy policy|Modern Slavery Act Transparency Statement|Sitemap|About US| Contact US: help@patsnap.com